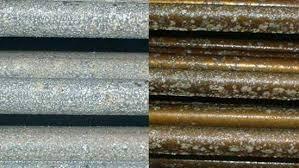
Rust inhibitors, also known as corrosion inhibitors, are specialized chemical compounds or materials designed to prevent or significantly slow the oxidation process that leads to rust and corrosion on metals. Rust, a common term for iron oxide, forms when metals containing iron, such as steel, are exposed to oxygen and moisture for extended periods. This process, while natural, can cause severe material degradation, reducing structural integrity, functionality, and aesthetic appeal. Left unchecked, rust can result in costly repairs, equipment failures, and even safety hazards in critical applications.
The role of rust inhibitors is to act as a protective shield for metals, either by creating a physical barrier that blocks corrosive agents or by chemically altering the reaction between the metal and environmental factors like water, oxygen, or salt. These inhibitors are indispensable in industries where metal longevity and performance are critical. For instance, in the automotive and aerospace sectors, rust inhibitors ensure the durability and reliability of vehicles and aircraft, safeguarding against wear and tear. In construction, they protect vital infrastructure components, such as beams and reinforcements, from premature corrosion. Even in household applications, rust inhibitors play a vital role in preserving everyday tools, appliances, and outdoor furniture.
With the ever-growing emphasis on sustainability and cost-efficiency, the use of rust inhibitors has gained prominence across various industries. They not only extend the lifespan of metal products but also help reduce maintenance costs and minimize environmental impact by decreasing the need for replacements or resource-intensive repairs. As a result, rust inhibitors are at the forefront of efforts to combat corrosion, a persistent challenge that affects nearly every industry relying on metallic materials.
What is Rust?
What is Rust?
Before delving into rust inhibitors, it is crucial to comprehend the nature of rust itself. Rust is the product of a chemical reaction known as oxidation, which occurs when iron reacts with oxygen and moisture in the environment. The resulting compound, iron oxide (Fe₂O₃), forms a flaky, reddish-brown layer on the surface of the metal. This process is most common in iron and its alloys, such as steel, and becomes more pronounced with prolonged exposure to water and air.
The formation of rust is not merely an aesthetic issue; it has far-reaching implications for the functionality and longevity of metallic structures. Rust weakens the structural integrity of metals, making them brittle and prone to failure. In machinery, it can impair moving parts, reducing efficiency and potentially leading to operational breakdowns. In vehicles, rust compromises safety by eroding critical components like frames and brake lines. Similarly, in infrastructure, rust can lead to catastrophic consequences, such as the weakening of bridges, pipelines, and building reinforcements.
Understanding the mechanics and consequences of rust underscores the importance of effective rust prevention strategies. By recognizing how and why rust forms, industries can take proactive measures, such as employing rust inhibitors, to protect metal assets and ensure their durability and safety over time.
What are Rust Inhibitors?
What are Rust Inhibitors?
Rust inhibitors are specialized chemical compounds designed to prevent or slow down the oxidation process that causes rust formation on metal surfaces. Oxidation occurs when metals, particularly iron and its alloys like steel, come into contact with moisture and oxygen, leading to the development of rust, a form of iron oxide. Rust inhibitors mitigate this process by creating a protective barrier that reduces the metal's exposure to corrosive elements, thereby extending its lifespan and preserving its integrity.
These inhibitors are available in various forms to suit diverse applications and industries. Common forms include rust-preventive paints and coatings, which form a physical shield over the metal surface to block moisture and air. Additives for oils and fuels are also widely used, particularly in automotive and industrial machinery, where they enhance lubrication while protecting metal components from rust. Other formulations, such as water-based sprays and powders, offer flexibility for temporary or long-term protection depending on the specific needs.
The versatility of rust inhibitors makes them indispensable across sectors, from construction and transportation to manufacturing and household applications. Whether used to safeguard large industrial machinery, preserve the integrity of pipelines, or protect everyday tools, rust inhibitors play a pivotal role in maintaining the performance, safety, and longevity of metal assets.
How Do Rust Inhibitors Work?
How Do Rust Inhibitors Work?
Rust inhibitors operate through various mechanisms tailored to their chemical composition and intended application, effectively protecting metals from corrosion in diverse environments. Here are the primary ways in which rust inhibitors function:
Barrier Protection
Many rust inhibitors create a physical barrier on the metal surface to block contact with moisture, oxygen, and other corrosive agents. This barrier can take the form of paints, coatings, waxes, or thin films. By isolating the metal from the environment, these inhibitors minimize exposure to elements that trigger oxidation. Barrier protection is widely used in automotive finishes, industrial machinery, and outdoor metal structures.Sacrificial Anode
Some rust inhibitors use a principle known as cathodic protection, employing a sacrificial anode made of a more reactive metal, such as zinc or magnesium. The sacrificial anode corrodes preferentially, sparing the protected metal from rust. This technique is common in marine and underground applications, such as protecting ships, pipelines, and storage tanks.Corrosion Inhibition
Chemical corrosion inhibitors work by interacting with the metal surface or the surrounding environment. These inhibitors can form a protective chemical film on the metal, neutralize corrosive agents like acids, or reduce the electrochemical reactions that cause rust. They are often added to lubricants, fuels, and cooling systems to safeguard internal components of engines and machinery.Passivation
Some rust inhibitors enhance the formation of a passive oxide layer on the metal surface, which is stable and less reactive than the base metal. This passivation layer acts as a shield, preventing further oxidation. Passivating inhibitors are particularly effective for stainless steel and other alloys prone to localized corrosion, such as pitting or crevice corrosion.
By employing these mechanisms, rust inhibitors address a wide range of corrosion challenges across industries, ensuring the longevity and reliability of metal components and structures. Whether in industrial, marine, automotive, or household settings, rust inhibitors are essential tools in combating the pervasive issue of metal corrosion.
Types of Rust Inhibitors
Types of Rust Inhibitors
Rust inhibitors can be categorized based on their chemical composition and how they function to protect metals. Below are the main types, each with its unique properties and applications:
1. Organic Rust Inhibitors
Organic rust inhibitors are derived from carbon-based compounds and are often used to create protective films on metal surfaces. Their effectiveness is due to their ability to chemically interact with metals and form stable, non-reactive layers. Common examples include:
- Amines: These compounds adsorb onto metal surfaces, forming a thin protective layer that blocks moisture and oxygen. They are widely used in lubricants and industrial systems to prevent rust.
- Carboxylic Acids: These acids react with metal ions to create stable complexes, reducing the availability of free ions that contribute to corrosion. They are often used in formulations for coatings and oils.
2. Inorganic Rust Inhibitors
Inorganic rust inhibitors are typically metal salts or oxides that provide corrosion resistance by forming protective compounds on metal surfaces. Examples include:
- Zinc Phosphate: Frequently used in industrial and automotive paints, zinc phosphate forms a protective barrier that inhibits rust formation and enhances adhesion for coatings.
- Chromates: Although highly effective at preventing corrosion, chromates are now less favored due to environmental and health concerns. Safer alternatives are being developed to replace them in various applications.
3. Volatile Corrosion Inhibitors (VCIs)
VCIs are compounds that release protective vapors. These vapors condense on metal surfaces, forming an invisible barrier against moisture and oxygen. Key features of VCIs include:
- Applications: Commonly used in packaging materials, VCIs are ideal for protecting metal parts during storage and transportation.
- Enclosed Protection: They are particularly effective in enclosed environments, such as sealed containers or storage units, where they can provide long-lasting protection.
4. Electrochemical Inhibitors
Electrochemical inhibitors work by altering the reactions that lead to corrosion, either by suppressing anodic or cathodic activity. These are often used in industrial systems such as pipelines, cooling systems, and marine environments. Examples include:
- Nitrites: Nitrites form a protective oxide layer on the metal surface, inhibiting corrosion in cooling systems and similar applications.
- Molybdates: Effective in alkaline environments, molybdates offer protection by stabilizing the metal surface and preventing rust-inducing reactions.
Applications of Rust Inhibitors:
Applications of Rust Inhibitors:
Rust inhibitors are used in a wide range of applications across various industries. Here are some common uses:
1. Automotive Industry:
In the automotive industry, rust inhibitors are used in paints, coatings, and underbody treatments to protect vehicles from corrosion. The harsh conditions that vehicles face, including exposure to moisture, road salt, and pollutants, make rust inhibitors essential for maintaining the longevity and appearance of cars.
2. Construction and Infrastructure:
Rust inhibitors are crucial in the construction industry, where steel and iron are commonly used in structures such as bridges, buildings, and pipelines. Protective coatings containing rust inhibitors are applied to steel reinforcements and structural components to prevent corrosion, ensuring the safety and durability of infrastructure.
3. Marine Applications:
In marine environments, metal structures and vessels are particularly susceptible to rust due to constant exposure to saltwater. Rust inhibitors, including sacrificial anodes and specialized coatings, are employed to protect ships, offshore platforms, and other marine equipment from corrosion.
4. Manufacturing and Machinery:
Manufacturing equipment and machinery often face harsh operating conditions that can lead to rust formation. Rust inhibitors are used in lubricants, oils, and protective coatings to extend the lifespan of machinery and reduce maintenance costs.
5. Electronics:
In the electronics industry, rust inhibitors are used to protect metal components from corrosion, which can lead to failure in electronic devices. Coatings and treatments that contain rust inhibitors help ensure the reliability and longevity of electronic products.
Benefits of Using Rust Inhibitors:
Benefits of Using Rust Inhibitors:
The use of rust inhibitors provides numerous benefits, making them indispensable across industries. These advantages include:
1. Extended Lifespan of Metal Components
Rust inhibitors protect metal surfaces from corrosion, significantly prolonging their useful life. This durability reduces the need for frequent replacements and repairs, ensuring the continued performance of machinery, vehicles, and infrastructure while minimizing operational disruptions.
2. Cost Savings
Investing in rust inhibitors is a cost-effective solution for combating corrosion-related damage. By preventing rust, businesses can avoid the expenses associated with equipment repairs, replacements, and downtime caused by rust-related failures. This proactive approach translates into long-term financial savings.
3. Improved Aesthetics
Rust often tarnishes the appearance of metal surfaces, diminishing their appeal. Rust inhibitors help maintain the visual quality of products, vehicles, and structures, which is particularly important in consumer-facing industries such as automotive, appliances, and construction. A rust-free appearance enhances the perceived value and quality of goods.
4. Enhanced Safety
In industries where structural integrity is critical, such as construction, aerospace, and transportation, rust inhibitors play a vital role in preventing catastrophic failures caused by corrosion. By maintaining the strength and reliability of metal components, they contribute to overall safety and accident prevention.
5. Environmental Protection
Rust inhibitors support sustainability by reducing waste and resource consumption. By prolonging the lifespan of metal components, they decrease the demand for manufacturing new parts, which often requires significant energy and raw materials. This reduction in production helps lower the environmental impact associated with metal fabrication and disposal.
Conclusion:
Conclusion:
Rust inhibitors are essential tools in the fight against corrosion, providing effective protection for metal surfaces across various industries. By understanding the different types of rust inhibitors, their mechanisms of action, and their applications, businesses can make informed decisions about how to best protect their assets from rust. As technology continues to advance, the development of new and more effective rust inhibitors will play a crucial role in ensuring the longevity and reliability of metal components in an ever-changing environment. Investing in rust inhibitors is not just a matter of maintenance; it is a proactive approach to safeguarding the future of metal products and structures