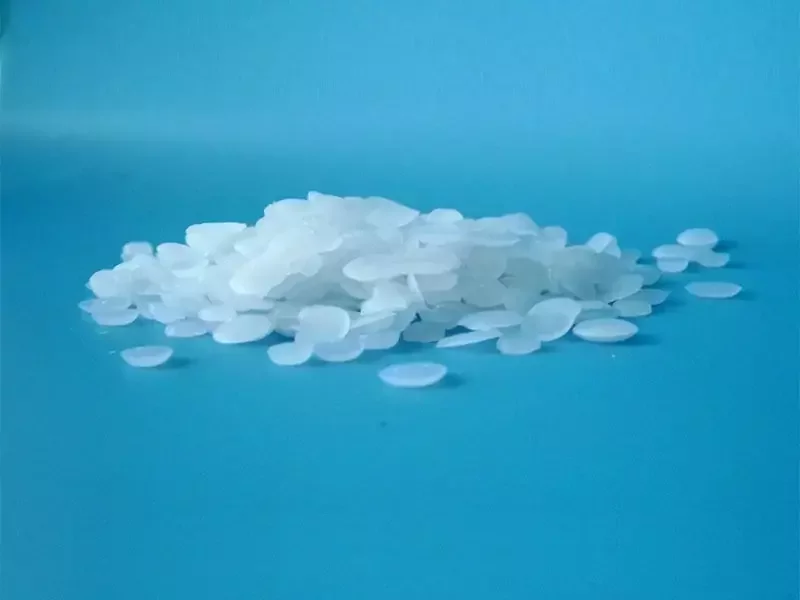
Wax deposition is a persistent issue in the oil and gas industry, posing significant operational challenges. When crude oil is extracted from reservoirs and transported through pipelines, temperature and pressure fluctuations cause the precipitation of high-molecular-weight paraffins. These paraffins solidify and accumulate on pipeline walls, leading to blockages, production inefficiencies, and increased maintenance costs. If not properly managed, wax deposition can cause complete pipeline shutdowns, resulting in substantial financial losses.
One of the most effective methods to combat wax deposition is the use of wax dispersants. These specialized chemical agents prevent the agglomeration and adhesion of wax particles, allowing them to remain suspended in the oil phase. This ensures smooth hydrocarbon flow, minimizing disruptions and enhancing production efficiency.
In this blog, we will delve deeper into the concept of wax dispersants, their working mechanisms, types, chemical compositions, applications, and best practices for effective usage.
Understanding Wax Deposition
Crude oil contains various hydrocarbons, including paraffin waxes, which can precipitate out when the temperature drops below the Wax Appearance Temperature (WAT). This leads to the accumulation of wax deposits in pipelines, storage tanks, and processing equipment, restricting flow and causing operational challenges.
Several factors contribute to wax deposition:
- Temperature drops: When crude oil moves through pipelines in colder environments, wax solidifies and adheres to surfaces.
- Pressure changes: Pressure drops during transportation can cause wax precipitation.
- Crude oil composition: Certain crude oils have higher wax content, making them more prone to deposition.
- Shear effects: The movement of crude oil through pipelines can lead to shear-induced crystallization, further accelerating wax formation.
- Flow velocity: Slower-moving crude oil tends to allow wax particles to settle, increasing deposit formation.
To combat these issues, industries use wax dispersants as a preventive and corrective solution, ensuring the optimal performance of transportation and processing systems.
What Are Wax Dispersants?
Wax dispersants are chemical additives designed to prevent and mitigate wax deposition in crude oil production and transportation. These dispersants contain surfactants and solvents that modify wax crystal formation, reducing their tendency to agglomerate and stick to pipeline walls or equipment surfaces. The effectiveness of a wax dispersant depends on its chemical formulation, the type of crude oil, and the operational conditions where it is applied.
Some common components of wax dispersants include:
- Nonionic surfactants: These help break down wax particles and disperse them in the crude oil.
- Solvents: Aid in dissolving wax and keeping it suspended in liquid hydrocarbons.
- Polymeric additives: Prevent wax aggregation and improve flowability.
How Do Wax Dispersants Work?
Wax dispersants are chemical additives designed to prevent wax deposition in crude oil pipelines and production systems. They work through a combination of mechanisms that modify wax behavior, ensuring smooth oil flow while minimizing blockages and maintenance requirements. Let’s explore these mechanisms in detail:
1. Crystal Modification
One of the primary functions of wax dispersants is altering the size and structure of wax crystals. Crude oil contains waxes that naturally tend to crystallize at lower temperatures, forming large, interlocking structures that adhere to pipeline walls and restrict flow. Dispersants interact with these wax molecules to:
Reduce the size of wax crystals, preventing the formation of large, rigid networks.
Modify the shape of crystals, making them more spherical or irregular instead of needle-like or plate-like structures that easily stick together.
Inhibit wax crystal growth, ensuring that even at low temperatures, the wax remains manageable and does not contribute to flow assurance problems.
By changing the morphology of wax crystals, dispersants keep them suspended in the oil rather than forming cohesive deposits.
2. Surface Adsorption
Wax dispersants contain surface-active agents that adhere to metal surfaces within pipelines and production equipment. This creates a protective barrier that:
Prevents wax molecules from adhering to pipeline walls and equipment surfaces.
Reduces the formation of wax deposits, which could otherwise lead to pipeline blockages and increased pressure drop.
Enhances the effectiveness of other flow assurance chemicals by maintaining a smooth pipeline surface, minimizing friction and buildup.
This mechanism is particularly effective in deepwater or cold environments where wax deposition is more pronounced.
3. Solubilization
Some dispersants contain solvents that help dissolve wax particles, maintaining their fluidity within the oil. This mechanism works by:
Reducing the tendency of wax molecules to aggregate into larger clusters.
Enhancing wax solubility in crude oil, preventing the formation of solid deposits.
Keeping wax components in a dispersed phase, allowing them to be carried along with the flowing oil rather than settling out and accumulating on surfaces.
Solubilization ensures that wax remains in liquid form or as a fine dispersion, reducing the risk of blockages and minimizing the need for mechanical interventions such as pigging or heating.
4. Dispersion Effect
Wax dispersants break down large wax agglomerates into smaller, more evenly distributed particles. This ensures that:
Wax remains suspended in the oil rather than settling and forming blockages.
Oil flow remains smooth, with a reduced risk of pipeline restrictions due to wax buildup.
The viscosity of the crude oil is optimized, preventing excessive thickening due to wax accumulation.
By dispersing wax into fine particles, dispersants help maintain a uniform distribution of wax throughout the crude oil, preventing localized deposits that can obstruct flow.
5. Emulsion Prevention
Water-in-oil emulsions can exacerbate wax deposition issues by creating a sticky matrix that enhances wax adhesion and accumulation. Some wax dispersants contain demulsifying agents that:
Prevent the formation of stable emulsions that trap wax and increase deposition rates.
Reduce the interaction between wax molecules and water droplets, ensuring that wax remains free-flowing.
Enhance the efficiency of separation processes, minimizing the presence of water that can contribute to operational challenges.
By controlling emulsions, dispersants ensure that wax-related issues are mitigated, further improving flow assurance and reducing maintenance needs.
Applications of Wax Dispersants
Wax dispersants play a critical role in preventing wax-related issues across multiple industries. While their most significant use is in the oil and gas sector, they are also essential in fuel processing, lubricants, and other industrial applications. Below is a detailed breakdown of their applications in different industries.
1. Oil & Gas Industry
The oil and gas industry heavily relies on wax dispersants to ensure uninterrupted operations and prevent costly blockages caused by wax deposition. Their applications include:
Pipeline Flow Assurance
Wax dispersants are injected into subsea and onshore pipelines to keep wax particles suspended in crude oil, preventing deposition along pipeline walls.
This helps maintain the efficiency of long-distance crude oil transportation, reducing the need for mechanical interventions such as pigging or heating.
Wellbore Treatment
In oil wells with high wax content, dispersants are applied to prevent wax buildup in tubing and downhole equipment.
This ensures optimal production rates and reduces the frequency of well shutdowns for wax removal operations.
Storage & Transportation
Crude oil storage tanks and transport vessels use dispersants to prevent wax settling at the bottom, maintaining uniform crude quality.
By keeping wax in suspension, dispersants reduce the need for heating systems and mechanical agitation in storage facilities.
Subsea Operations
In deepwater drilling environments, low temperatures accelerate wax deposition.
Dispersants help counteract these effects by modifying wax crystal structures and keeping them dispersed within the oil, ensuring smooth production flow.
2. Fuel Industry
Wax dispersants are essential in the fuel sector, particularly in cold climates where wax precipitation can impact fuel quality and performance.
Diesel & Jet Fuel Additives
Low temperatures can cause wax in diesel and jet fuel to crystallize, leading to clogged filters and engine malfunctions.
Dispersants prevent wax from agglomerating, ensuring smooth fuel flow in vehicles, aircraft, and industrial machinery.
Heating Oil Treatment
In heating systems, wax buildup can obstruct fuel lines and reduce combustion efficiency.
Dispersants keep the wax finely dispersed, ensuring consistent fuel flow and efficient heating.
3. Lubricant Manufacturing
Wax dispersants play a vital role in lubricant production by preventing wax-related viscosity issues.
Wax Control in Lubricants
Some lubricants contain waxes that can solidify under certain conditions, affecting performance.
Dispersants help maintain the fluidity of lubricants, ensuring smooth machinery operation in various temperature conditions.
Grease Formulation
In industrial greases, wax dispersants improve flow properties and prevent solidification, enhancing the consistency and usability of the grease
Benefits of Wax Dispersants
Wax dispersants offer several advantages, making them an essential component in petroleum processing and transportation:
✅ Enhanced Flow Assurance: Keeps pipelines and equipment free from wax buildup, ensuring uninterrupted oil flow.
✅ Reduced Maintenance Costs: Minimizes the need for mechanical cleaning, pigging, or chemical solvent flushing.
✅ Improved Operational Efficiency: Reduces production downtime caused by wax-related blockages.
✅ Optimized Crude Oil Transport: Helps maintain crude oil quality and reduces risks during storage and transportation.
✅ Eco-Friendly Solutions: Many modern wax dispersants are formulated with biodegradable components, reducing environmental impact.
✅ Prevention of Equipment Damage: Reduces wear and tear on pumps, valves, and storage tanks caused by wax buildup.
Choosing the Right Wax Dispersant
Choosing the right wax dispersant is essential to maintaining efficient oil flow, preventing wax buildup, and minimizing operational disruptions. Several factors influence the effectiveness of a dispersant in different environments.
1. Crude Oil Composition
The paraffin wax content in crude oil plays a crucial role in determining the required dispersant strength.
High-wax-content crude oils demand dispersants with stronger solubilizing and dispersing capabilities.
The presence of asphaltenes and resins can affect wax behavior, necessitating a dispersant compatible with the crude’s chemical profile.
2. Operating Temperature
Some dispersants are formulated to work in extreme cold conditions, such as deepwater or Arctic environments, where wax crystallization occurs more rapidly.
In warmer environments, dispersants with lower pour points may be sufficient.
The dispersant should remain effective across the temperature range experienced during crude oil transportation and storage.
3. Pipeline and Storage Conditions
Pipeline diameter and length influence the dispersant’s dosage and dispersion efficiency.
Long-distance pipelines may require dispersants with sustained effectiveness to prevent wax buildup over extended travel times.
Storage duration is also a factor—if crude oil remains in tanks for long periods, a dispersant that maintains long-term wax dispersion is essential.
4. Compatibility with Other Chemical Treatments
Wax dispersants should not interfere with other additives used in crude oil processing, such as corrosion inhibitors, demulsifiers, or drag-reducing agents.
Some dispersants may react with these chemicals, reducing overall effectiveness or causing operational issues.
Laboratory testing ensures that the selected dispersant works in harmony with existing chemical treatments.
5. Environmental Considerations
Some wax dispersants contain solvents or surfactants that can have environmental implications.
Eco-friendly formulations are preferred in offshore and environmentally sensitive areas to reduce ecological risks.
Regulatory compliance is crucial, ensuring that the dispersant meets local and international environmental standards.
Best Practices for Wax Dispersant Application
- Proper Dosage: Overuse can lead to unnecessary costs, while underuse may be ineffective.
- Early Intervention: Applying dispersants before wax deposition occurs is more effective than removing existing deposits.
- Regular Monitoring: Conducting flow assurance tests ensures optimal dispersant performance.
- Customized Formulation: Selecting a dispersant tailored to the crude oil type improves efficiency.
- Temperature Management: Ensuring dispersants function effectively within the temperature range of the operational environment.
Conclusion
Wax dispersants are a vital solution for industries facing wax deposition issues, particularly in oil and gas production, transportation, and refining. By using the right dispersants, companies can significantly reduce operational challenges, cut maintenance costs, and ensure efficient hydrocarbon flow. With continuous advancements in chemical formulations, the future of wax dispersants promises even greater efficiency and sustainability.
If you are in the oil and gas sector or any industry affected by wax buildup, investing in high-quality wax dispersants can improve your operations and bottom line.
Would you like to learn more about specific wax dispersant formulations or case studies? Let us know in the comments!