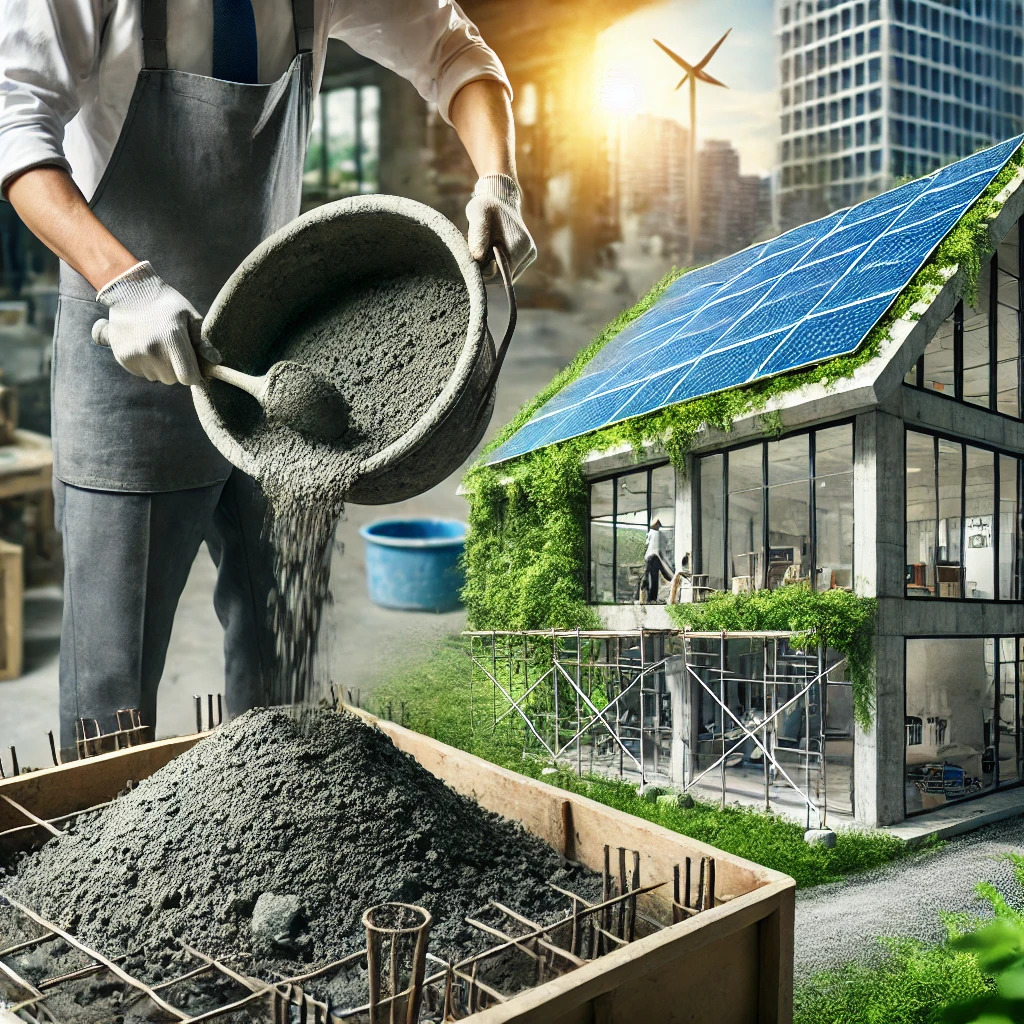
Concrete is one of the most widely used construction materials in the world, known for its strength, durability, and versatility. However, the performance of concrete can be significantly influenced by the properties of its components, particularly cement. To enhance the performance of concrete, various additives are incorporated into the mix. This blog will explore what cement additives are, their types, functions, benefits, and their role in sustainable construction practices.
What Are Cement Additives?
Cement additives, also referred to as admixtures, play a crucial role in enhancing the properties of concrete. These additives are specially formulated materials that are added to the concrete mix to modify and improve its characteristics, making it suitable for a wide range of construction needs. The inclusion of cement additives can occur at different stages of the concrete production process, either during the mixing of raw materials at the batching plant or directly at the job site, depending on the specific requirements of the project.
The primary objective of cement additives is to improve the performance and functionality of concrete, addressing key attributes such as workability, strength, durability, and setting time. By adding certain additives to the mix, contractors can customize the concrete's properties to meet the demands of various environmental conditions, structural loads, and construction techniques. As concrete is one of the most commonly used materials in the construction industry, cement additives have a significant impact on the efficiency, sustainability, and long-term performance of the material.
Types of Cement Additives
Cement additives are broadly classified into two main categories: chemical additives and mineral additives. Each type serves specific purposes in altering the physical and chemical properties of concrete. These categories can be used individually or in combination to achieve the desired concrete performance.
1. Chemical Additives
Chemical additives are substances that modify the chemical reactions occurring in the cement mix. These additives are typically introduced in small amounts and have a profound effect on the concrete’s workability, strength development, and setting characteristics. There are several types of chemical additives, each serving a different purpose:
Plasticizers (Water Reducers): These are used to improve the workability of concrete by reducing the amount of water required for mixing while maintaining the same consistency. This helps achieve a more flowable mixture, reducing the risk of segregation. In some cases, superplasticizers, which are more potent than normal plasticizers, are added to achieve higher workability.
Accelerators: Accelerating admixtures are used to speed up the setting and hardening process of concrete, which is particularly useful in cold weather conditions where concrete would otherwise take longer to set. Common accelerators include calcium chloride, which promotes faster hydration of cement particles, resulting in quicker strength gain.
Retarders: Retarding agents slow down the setting time of concrete, providing more time for handling and placement in hot weather. This is particularly beneficial when transporting and pouring large volumes of concrete, ensuring that it does not set prematurely before it can be properly mixed and poured.
Air-Entraining Agents: These admixtures create microscopic air bubbles within the concrete mix, which improves the concrete’s resistance to freeze-thaw cycles. This is especially important in areas where concrete is exposed to harsh weather conditions, such as freezing temperatures and moisture. The air bubbles provide space for water to expand during freezing, reducing the risk of cracks and damage.
Corrosion Inhibitors: Corrosion-inhibiting additives are used to protect the steel reinforcement in concrete from corrosion due to exposure to moisture and other environmental factors. These additives are particularly important for structures exposed to harsh conditions, such as marine environments or areas with high salt content.
Shrinkage Reducing Agents: These additives are designed to minimize the shrinkage that occurs as concrete dries and hardens. By reducing shrinkage, these agents help prevent the formation of cracks in the finished concrete, improving its durability and overall lifespan.
2. Mineral Additives
Mineral additives are finely ground materials added to the cement mix to improve its strength, durability, and other properties. These additives are typically naturally occurring materials or byproducts of other industrial processes. Some common mineral additives include:
Fly Ash: A byproduct of burning coal in power plants, fly ash is a commonly used mineral additive in concrete. It improves the workability and durability of concrete while also reducing its environmental impact by reusing industrial waste. Fly ash can enhance concrete’s resistance to sulfate attack and alkali-silica reaction, as well as reduce the heat of hydration in mass concrete structures.
Silica Fume: Silica fume is a byproduct of producing silicon metal or ferrosilicon alloys. It is known for its high pozzolanic properties, which significantly improve the strength and durability of concrete. Silica fume is commonly used in high-performance concrete applications, including structures that require enhanced resistance to abrasion, chemical attack, and extreme weather conditions.
Ground Granulated Blast Furnace Slag (GGBFS): GGBFS is a byproduct of the steel manufacturing process, and when used as a cement additive, it improves the workability, strength, and durability of concrete. Concrete made with GGBFS is highly resistant to corrosion and sulfate attack, making it ideal for use in structures exposed to aggressive environments, such as marine structures or sewage treatment plants.
Natural Pozzolans: These are naturally occurring materials such as volcanic ash or calcined clays, which, when finely ground, can react with calcium hydroxide in the presence of water to form compounds that contribute to the strength of the concrete. Pozzolans can enhance the long-term durability and resistance of concrete to weathering and chemical attacks.
Limestone Powder: This mineral additive is used to increase the workability and reduce the cost of concrete production. It can also improve the long-term strength and durability of concrete, especially when used in combination with other mineral additives like fly ash or silica fume.
Benefits of Cement Additives
Improved Workability: Additives such as plasticizers and superplasticizers enhance the flowability of concrete, making it easier to handle, mix, and place without compromising the concrete's strength or durability.
Faster Setting and Hardening: Accelerators speed up the setting time of concrete, reducing delays and improving the efficiency of construction projects. This is particularly useful in cold climates or situations where rapid construction is required.
Enhanced Durability: Many additives, such as air-entraining agents and mineral additives like fly ash and silica fume, improve the long-term durability of concrete, making it more resistant to environmental factors such as moisture, freeze-thaw cycles, and chemical attacks.
Cost-Effectiveness: The use of mineral additives like fly ash and slag can reduce the amount of cement required in the mix, lowering material costs while still maintaining or improving concrete performance. Additionally, they can help reduce the carbon footprint of concrete by using industrial byproducts.
Customized Performance: By selecting the appropriate combination of chemical and mineral additives, concrete can be tailored to meet the specific needs of a project, such as higher strength, improved resistance to chemicals, or better workability under challenging conditions.
The Role of Cement Additives in Sustainable Construction
Sustainable construction practices are gaining significant traction as the world faces the mounting challenges of climate change, resource depletion, and environmental degradation. These practices are essential for ensuring that the built environment can meet the needs of present and future generations without compromising the planet’s health. Cement additives, often overlooked in the broader conversation, are playing an increasingly vital role in promoting sustainability in the construction industry. By incorporating various types of additives, especially mineral additives, cement producers and contractors can reduce environmental impacts while maintaining or even enhancing the performance of concrete.
Here’s how cement additives contribute to sustainability in construction:
1. Reducing Carbon Emissions
The production of cement is one of the largest industrial sources of CO2 emissions worldwide. Cement manufacturing involves high-energy processes, such as heating limestone to produce clinker, which releases a significant amount of carbon dioxide as a byproduct. Cement additives, particularly mineral additives like fly ash, slag, and silica fume, can replace a portion of the cement in concrete mixes. This substitution leads to a reduction in the amount of cement required, thereby decreasing the carbon footprint associated with concrete production.
Fly Ash and Slag: These by-products of coal combustion and steel manufacturing, respectively, are rich in silica and alumina. When incorporated into the mix, they react with lime to form cementitious compounds, similar to the reaction that occurs when cement itself hydrates. This process, known as pozzolanic activity, not only reduces the amount of cement needed but also reduces the energy-intensive processes involved in producing traditional cement. By using these industrial by-products, cement manufacturers can significantly lower the CO2 emissions generated from raw material extraction and cement production.
Life Cycle Emission Reduction: Studies have shown that replacing a portion of cement with mineral additives can reduce the carbon footprint of concrete by up to 50%. The use of such additives is considered one of the most effective strategies for mitigating climate change within the construction industry.
2. Enhancing Resource Efficiency
The construction industry is notorious for its high consumption of raw materials, with cement being one of the largest contributors. By optimizing the use of cement through the inclusion of additives, the demand for raw materials is reduced, leading to more efficient resource use. Additives like fly ash, slag, and natural pozzolans help improve the properties of concrete, allowing it to meet the desired strength and durability standards with less cement content. This efficiency translates into the conservation of raw materials, less energy consumption in cement production, and reduced environmental degradation from mining and extraction activities.
Optimized Concrete Mixes: Additives can enhance the workability, strength, and durability of concrete, which means less material is required to achieve the same performance. For example, silica fume can improve concrete’s strength and durability, allowing for a reduction in the overall amount of cement used without compromising the structural integrity of the building.
Cost Efficiency: The reduced consumption of cement also leads to cost savings in construction projects. While the initial cost of mineral additives like fly ash may be higher, the long-term benefits—both environmental and financial—are substantial. Additionally, the improved durability and performance of the concrete can result in fewer repairs and maintenance costs over the lifetime of the structure.
3. Promoting Recycling
The incorporation of industrial by-products such as fly ash, slag, and rice husk ash into concrete mixes directly supports the concept of recycling and waste reduction. In a traditional, linear economy, these by-products would be discarded as waste, contributing to landfill issues and environmental pollution. However, by using these materials in concrete production, we can reduce waste while simultaneously creating valuable construction materials.
Circular Economy: Cement additives derived from industrial by-products support the principles of a circular economy, which aims to minimize waste and make the most of available resources. Instead of treating these materials as waste, they are repurposed and integrated into concrete, thus reducing the need for virgin raw materials and promoting sustainability.
Waste-to-Resource Innovation: For instance, fly ash is an abundant by-product of coal combustion in power plants, and slag is generated during the production of steel. By diverting these materials from landfills and incorporating them into concrete, the construction industry can actively contribute to the reduction of industrial waste. This also lowers the environmental impact of other industries, such as power generation and steel production, by creating a viable and beneficial use for their by-products.
4. Improving Energy Efficiency
Energy efficiency is an important aspect of sustainable construction. Concrete structures, especially those used in residential and commercial buildings, can play a significant role in minimizing energy consumption over their lifecycle. Cement additives, by improving the performance and durability of concrete, can contribute to the creation of energy-efficient buildings.
Thermal Mass: Concrete’s ability to absorb and store heat—known as thermal mass—can be enhanced with the use of certain cement additives. By adjusting the properties of the concrete, additives can help regulate the temperature inside buildings, reducing the need for heating and cooling. This is particularly beneficial in regions with extreme weather conditions.
Durability and Longevity: Concrete with enhanced durability, resulting from the use of additives like fly ash and silica fume, requires less maintenance and fewer repairs over time. More durable concrete structures are less likely to deteriorate from weathering, corrosion, or chemical attacks, thus reducing the need for frequent refurbishing. The energy required for these repairs and replacements is therefore minimized.
Reduced Energy Use in Construction: The incorporation of mineral additives can also reduce the overall energy use in the production and transportation of materials. For example, the use of recycled fly ash in place of cement reduces the need for high-temperature processing, which is energy-intensive. Similarly, longer-lasting concrete structures that require less maintenance or replacement contribute to energy savings throughout their lifespan.
Conclusion
Cement additives are a vital tool in promoting sustainable construction practices. By reducing carbon emissions, enhancing resource efficiency, promoting recycling, and improving energy efficiency, these additives help reduce the environmental impact of concrete while maintaining or improving its performance. The construction industry is at a critical juncture, and sustainable practices such as the use of cement additives are essential for mitigating climate change, conserving natural resources, and ensuring the longevity of structures. As demand for more sustainable solutions grows, the role of cement additives in supporting eco-friendly construction practices will only become more significant, contributing to a more resilient and environmentally responsible built environment.