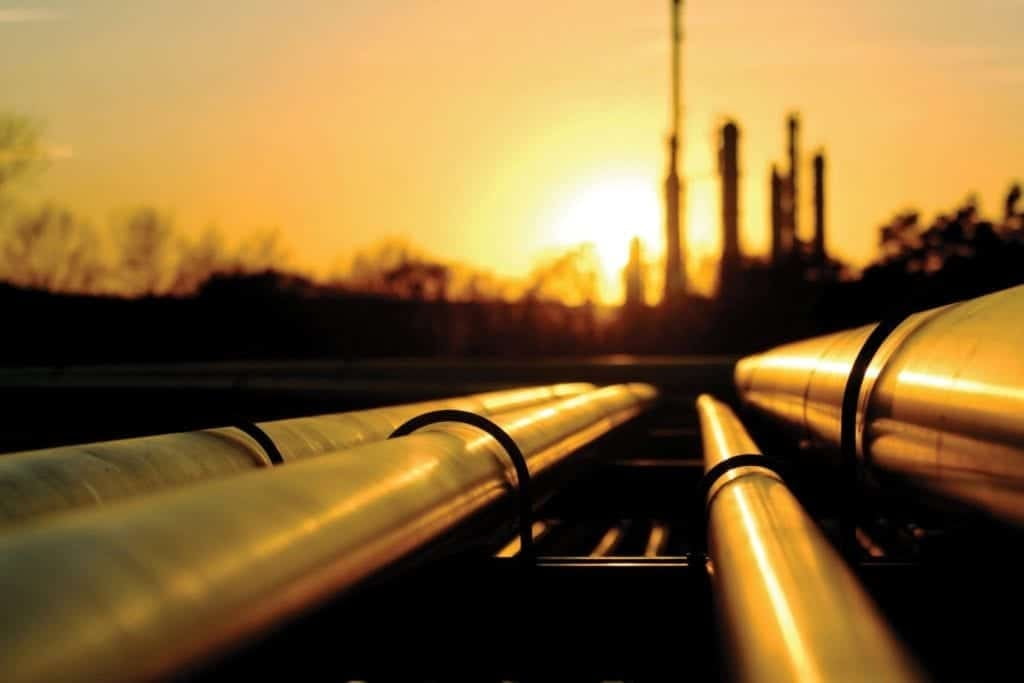
To combat this, companies utilize corrosion inhibitors, which are chemical compounds that delay or stop the rusting process. These inhibitors function by forming a protective barrier on the metal surface or by chemically modifying the conditions that induce corrosion, thereby protecting assets and extending the life of equipment. The use of corrosion inhibitors is especially important in large-scale companies because it can prevent catastrophic failures, assure smooth operations, and lower maintenance costs.
What is Corrosion Inhibitors?
A corrosion inhibitor is a chemical ingredient or compound that, when mixed with a liquid or gas, slows the rate of corrosion of a material, typically metal. Corrosion inhibitors function by either creating a protective barrier on the metal's surface or neutralizing corrosive chemicals in the environment. This helps to prevent or slow the electrochemical reactions that lead to corrosion.
In this article, we'll investigate ten different types of corrosion inhibitors and discuss how they operate to protect metal surfaces across many industries, offering long-term
1. Anodic Inhibitors (Passivating Inhibitors)
1. Anodic Inhibitors (Passivating Inhibitors)
Anodic inhibitors, also known as passivating inhibitors, are chemical substances that block the anodic reaction in corrosion, which occurs when metal loses electrons and begins to deteriorate. These inhibitors function by producing a protective oxide layer on the metal surface, preventing oxidation and reducing exposure to corrosive substances. By increasing the corrosion potential, anodic inhibitors drive the metal into a passive state, making it less reactive and more resistant to corrosion. Anodic inhibitors include chromates, nitrites, and molybdates, which are commonly employed in industries such as water treatment, vehicle cooling systems, and oil/gas pipelines. These inhibitors are vital in preserving metals in severe settings, and help to extend the Increase equipment lifespan, lower maintenance expenses, and avoid operational problems.
2. Cathodic Inhibitors
2. Cathodic Inhibitors
In order to prevent corrosion, cathodic inhibitors work by obstructing the cathodic reaction, which normally entails the reduction of oxygen or hydrogen ions in a corrosive environment. Cathodic inhibitors stop this process from happening, which lowers the metal's overall propensity to lose electrons and stops chemical deterioration. These inhibitors minimize corrosion by changing the electrochemical environment or by creating a protective coating on the metal surface. Polyphosphates, zinc, and phosphates are examples of common cathodic inhibitors. Zinc ions, for instance, react with water to coat the metal surface in a protective layer that lessens the metal's susceptibility to corrosion. This technique is particularly helpful in protecting pipelines, industrial equipment, and water systems against corrosion.
3. Mixed Inhibitors
3. Mixed Inhibitors
By mixing anodic and cathodic inhibitors, mixed inhibitors efficiently reduce both types of corrosion-causing processes and offer dual protection. These inhibitors block the anodic oxidation and cathodic reduction processes of the metal in a balanced manner. Typical combined inhibitors, including silicate compounds and organic amines, create a protective film that covers the whole metal surface and provides complete corrosion resistance. The likelihood of concentrated metal deterioration, such as localized pitting or crevice corrosion, is reduced by this general protection. In many different industries, where consistent metal surface protection is essential to avoiding damage and prolonging equipment life, mixed inhibitors are commonly utilized pipelines as well as industrial apparatus.
4. Volatile Corrosion Inhibitors (VCIs)
4. Volatile Corrosion Inhibitors (VCIs)
Chemical substances known as volatile corrosion inhibitors (VCIs) shield metal surfaces by releasing vapors into the atmosphere, which subsequently cover the metal in a thin layer of molecules. The metal is shielded from the environment's corrosive substances and moisture by this layer of protection. When it is impossible to apply inhibitors directly, like in confined quarters or during transit, VCIs are very helpful. Common VCIs that provide efficient corrosion prevention include hexamethylenetetramine and dicyclohexylamine nitrite, which evaporate and settle on the metal surface. These inhibitors are frequently employed in the aerospace industry, for the packaging and transportation of metal components, and for the storage of spare parts and machinery pipelines.
5. Organic Inhibitors
5. Organic Inhibitors
In acidic settings, such as those found in the oil and gas sectors, where metals must withstand hostile conditions during the drilling and refining processes, organic corrosion inhibitors are mainly employed. These inhibitors attach themselves to the metal surface as atoms of nitrogen, oxygen, or sulfur, creating a barrier that keeps out corrosive attacks. Azole, imidazoline, and amines are common examples of highly potent and diverse chemical inhibitors. They are a popular option for avoiding corrosion in a variety of industrial applications due to their capacity to offer robust protection in such harsh settings.pipelines and parts.
6. Inorganic Inhibitors
6. Inorganic Inhibitors
Metal salts, which coat or mask the metal surface to aid in passivation or react with corrosive species in the environment to neutralize them, are the main component of inorganic inhibitors. Silicates, phosphates, and chromates are common chemical compounds that are employed as inorganic inhibitors because they work well in both neutral and acidic media. When compared to organic inhibitors, these inhibitors offer a more ecologically friendly option, which makes them the go-to option for many industrial applications. They are widely used to prevent corrosion in metals on a big scale due to their efficacy and flexibility in various situations.
7. Precipitation Inhibitors
7. Precipitation Inhibitors
The mechanism by which precipitation inhibitors work is to build insoluble compounds that cover metal surfaces in corroding environments, providing a protective layer. These inhibitors' main ingredients, magnesium hydroxide and calcium carbonate, efficiently coat the metal in aqueous settings. These compounds work as a barrier to assist stop corrosion and scale, two problems that are frequently linked in many industrial applications. In the boiler and heat exchanger sectors, where preserving the integrity of metal surfaces is essential for long-term and effective operation, precipitation inhibitors are very useful.
8. Chelating Inhibitors
8. Chelating Inhibitors
Chelating inhibitors, also known as sequestering agents, function by forming stable complexes with metal ions present in a corrosive environment, thereby preventing these ions from reacting with other corrosive species. This chelation process helps to minimize the rate of corrosion by keeping metal ions in a water-soluble form, which reduces their reactivity. Common examples of chelating inhibitors include EDTA (ethylene diamine tetra-acetic acid) and NTA (nitrilotriacetic acid). These inhibitors are particularly effective in systems where iron or copper ions are present, as they prevent the formation of harmful corrosion products that can lead to metal degradation. By stabilizing metal ions and reducing their corrosive potential, chelating inhibitors play a crucial role in protecting metal surfaces in various industrial applications.
9. Film-Forming Inhibitors
9. Film-Forming Inhibitors
Inhibitors of film formation work by covering the metal surface with a thin layer of protection that keeps corrosive substances from coming into direct contact with the metal. The majority of these inhibitors are organic substances that attach themselves to the surface of the metal to create a barrier that strengthens corrosion resistance. Fatty acids, esters, and amides are common examples of film-forming inhibitors; they are a part of an inhibitory series that successfully lowers corrosion rates. These inhibitors are frequently employed in oilfield operations to assist shield metal components from corrosive substances and harsh environmental conditions. They are especially useful in offshore oil rigs and during the transportation of crude oil.
10. Oxidizing Inhibitors
10. Oxidizing Inhibitors
Oxidizing inhibitors work by encouraging the development of a stable oxide layer to shield metal surfaces from corrosion. These inhibitors include substances that catalyze oxidation processes that would normally happen more slowly, such as chromates and nitrates. Consequently, a film of protection forms, keeping the metal safe from additional harm. Oxidizing inhibitors are widely utilized in a variety of industrial applications where metals are exposed to oxygen-rich conditions. They are especially effective in neutral and moderately acidic environments. They are useful for protecting metal components in conditions where corrosion is a problem because of their capacity to promote the development of protective layers.
Conclusion
Corrosion inhibitors play a crucial role in extending the lifespan of metals used across various industries, including oil, gas, water treatment, and chemical processes. These inhibitors are selected based on their compatibility with specific environments and conditions, significantly minimizing damage and reducing maintenance costs while enabling safe and efficient operations. From anodic inhibitors to oxidizing inhibitors, each type offers unique benefits and protection mechanisms tailored to the corrosive environment at hand. This diversity allows for the development of more effective corrosion management strategies, ultimately saving time, resources, and money for industries. By implementing the appropriate inhibitors, organizations can safeguard their assets and ensure operational continuity in challenging conditions.