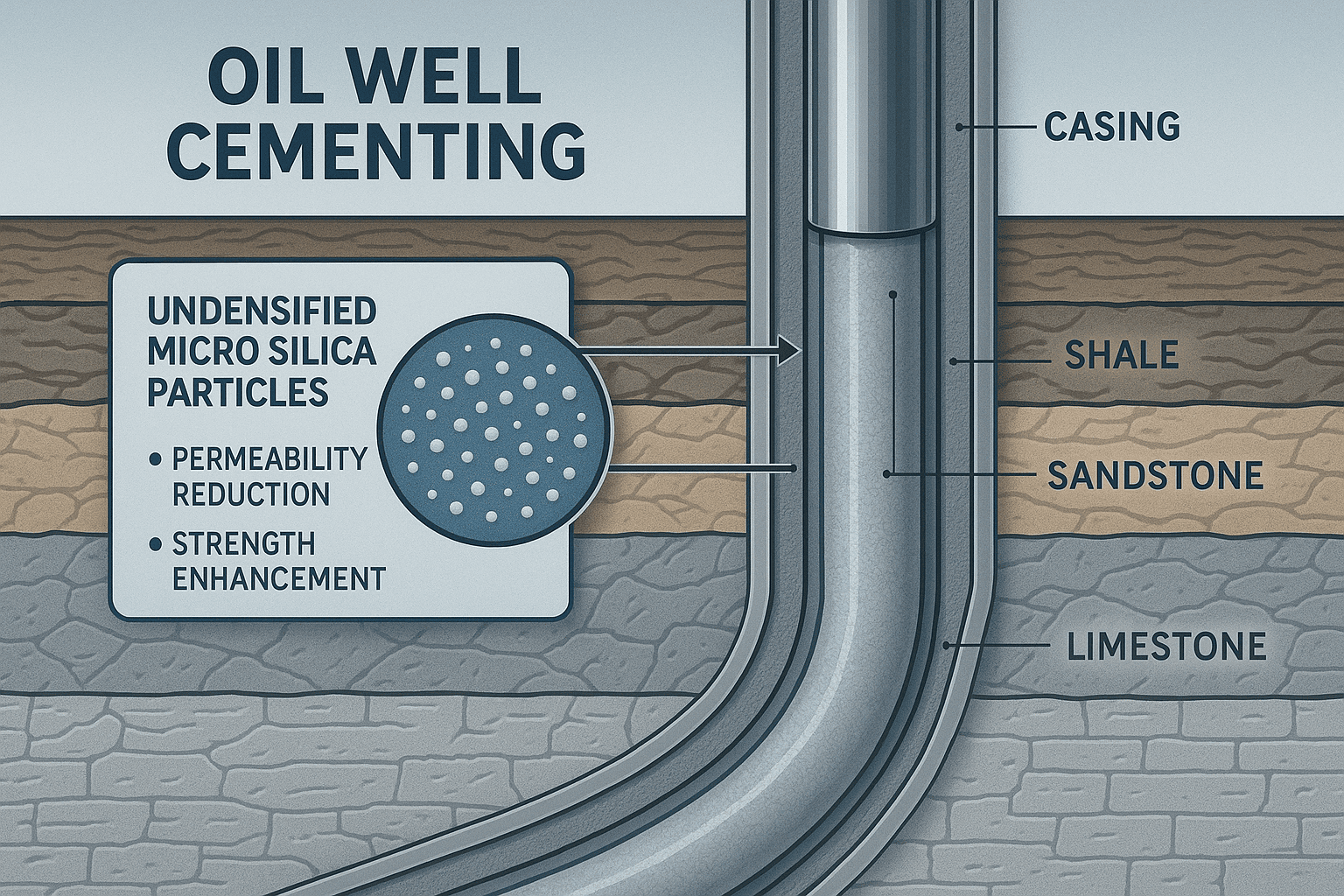
Undensified micro silica might not be a household name, but in the oil and gas industry, it's one of the most impactful materials used in cementing operations. With increasing demand for deeper wells, high-pressure and high-temperature (HPHT) drilling, and greater environmental responsibility, oilfield engineers are turning to specialized additives like undensified micro silica to enhance well integrity and performance.
In this article, we explore everything you need to know about undensified micro silica: what it is, why it's used, how it works, its key applications in oil and gas, and the technical specifications that make it a must-have material for any serious oilfield operation.
What Is Undensified Micro Silica?
Undensified micro silica, also known as silica fume, is a byproduct of the production of silicon and ferrosilicon alloys. It is made up of ultra-fine, amorphous silicon dioxide particles. While it's used across a variety of industries, undensified micro silica plays a crucial role in oil well cementing applications.
What sets undensified micro silica apart is its incredibly fine particle size. It has a surface area of about 20,000 m²/kg, which is roughly 100 times finer than cement particles. This makes it highly reactive and perfect for enhancing cement slurry performance.
Unlike densified micro silica, which is agglomerated for easier transportation and storage, undensified micro silica remains in its fine, fluffy form, allowing for better dispersion and reactivity when added to cement.
Why Is It Important in Oil & Gas?
Oil and gas wells are subject to some of the harshest environments imaginable. The cement used to isolate zones and secure casing must withstand extreme pressures, high temperatures, corrosive chemicals, and shifting geological formations.
Undensified micro silica improves several aspects of cement performance:
Reduces Permeability: The fine particles fill in the tiny voids in the cement matrix, significantly reducing its permeability.
Improves Strength: It reacts with calcium hydroxide to form additional calcium silicate hydrate (C-S-H), which gives cement its strength.
Resists Chemical Attack: It improves the resistance of cement to sulfates, chlorides, and other aggressive agents.
Prevents Gas Migration: It creates a denser cement sheath, reducing the chance of gas migration post-cementing.
Technical Specifications
Here's a snapshot of the key properties of undensified micro silica used in oil and gas cementing:
S. No. | Parameter | Test Result | Unit | Test Protocol |
1 | Level of SiO₂ | 90.02 | % | IS 67:1998 |
2 | Fineness | 0.2 | µM | IS 3339 (1975) |
3 | Specific Gravity | 2.3 | g/cm³ | IS 3018:1977 |
4 | Bulk Density | 257 | kg/m³ | IS 15388 (2003) |
5 | Loss on Ignition at 800°C | 3.7 | % | IS 67:1998 |
6 | Moisture Content | 1.3 | % | IS 67:1998 |
These numbers are more than just data points. They define the quality, consistency, and efficiency of micro silica in oil well cementing applications.
1. Oil Well Cementing: Building a Stronger Foundation
Cementing ensures that different zones in the formation are isolated, casing is properly supported, and the wellbore is shielded from corrosive fluids. The inclusion of undensified micro silica in the cement slurry significantly enhances its overall performance:
Increased Compressive Strength
Micro silica reacts pozzolanically with calcium hydroxide (CH), a byproduct of cement hydration, to form additional calcium silicate hydrate (C-S-H) gel. This secondary reaction boosts the microstructure of the set cement, resulting in much higher compressive strength. This is critical in maintaining well integrity under dynamic loads and thermal fluctuations.Reduced Free Water Content
The ultrafine particles fill in gaps between larger cement grains, improving particle packing density. This minimizes the amount of free water in the slurry, which is crucial for eliminating weak zones that can cause poor bonding and fluid migration.Improved Rheology and Pumpability
Despite lowering water-to-cement ratios, micro silica improves the flow properties of the slurry, making it easier to pump. This results in more efficient placement, better zonal coverage, and minimal fluid loss.
In complex wells, such as high-pressure, high-temperature (HPHT) applications, these enhancements make micro silica a non-negotiable additive in the cementing recipe.
2. Lightweight Cement Systems: Enhancing Stability in Weak Zones
Lightweight cements are indispensable when drilling through low-pressure, fractured, or depleted formations. However, traditional lightweight cements often compromise on strength and durability.
Undensified micro silica addresses these limitations:
Enhanced Strength-to-Weight Ratio
Even with reduced density, micro silica enhances the structural integrity of lightweight cement. Its pozzolanic reaction ensures the matrix remains strong, reducing risks of failure in fragile formations.Low Permeability for Better Zonal Isolation
Micro silica reduces the permeability of set cement by filling capillary pores and microvoids. This tighter matrix limits fluid ingress, protecting the formation and wellbore from crossflow and fluid losses.
Engineers can fine-tune the formulation to achieve specific compressive strength and flow properties, making lightweight systems both effective and reliable for challenging drilling scenarios.
3. Deepwater and HPHT Wells: Withstanding Extreme Conditions
Deepwater and HPHT wells are defined by high pressures (often exceeding 15,000 psi) and temperatures that can soar above 300°F (150°C). These environments demand cement systems with exceptional mechanical and chemical resilience.
Undensified micro silica brings key benefits:
Thermal Stability at Elevated Temperatures
Cement slurries containing micro silica exhibit high thermal resistance, retaining compressive strength and elasticity even under prolonged exposure to heat. This makes them ideal for deep and ultra-deep well applications.Resistance to Aggressive Formation Fluids
Saline, acidic, or CO₂-rich environments can degrade ordinary cement. Micro silica densifies the matrix, reducing permeability and making the cement less susceptible to chemical attack.Improved Elasticity
High elasticity reduces the risk of micro-annulus formation, especially when thermal expansion or casing movement occurs. Micro silica imparts flexibility to the set cement, helping it accommodate mechanical stresses without cracking.
In these frontier operations, micro silica isn’t just a performance enhancer—it’s a safeguard against failure.
4. Gas Migration Control: Securing the Wellbore Early
Gas migration is one of the most dangerous risks during well cementing. It occurs when formation gas invades the cement column before the slurry has developed sufficient strength to resist intrusion.
Micro silica plays a preventative role by:
Creating a Dense Cement Matrix
The extremely small particle size of micro silica (often <1 µm) allows it to fill voids and form a more compact, impermeable structure, limiting pathways for gas movement.Accelerating Initial Set and Strength Gain
Micro silica contributes to early strength development by accelerating the hydration process. This shortens the window during which gas can migrate into the unset slurry.Enhanced Gel Strength Development
Rapid gel strength build-up enables the cement to resist gas influx at earlier stages, effectively sealing off annular space before the cement fully hardens.
By minimizing the risk of gas migration, micro silica directly contributes to safer drilling operations and better environmental compliance.
5. Compatibility with Other Cement Additives: A Formulator’s Friend
Micro silica’s true strength lies in its versatility. It can be seamlessly integrated into a wide variety of cement formulations, making it suitable for different drilling environments and operational goals.
Retarders for High-Temperature Control
In HPHT applications, controlling the set time is crucial. Micro silica works well with retarders, ensuring that cement remains pumpable while still benefiting from strength enhancements.Dispersants for Improved Flowability
To maintain good rheology without increasing water content, dispersants are added to reduce slurry viscosity. Micro silica complements these agents by improving flow characteristics while maintaining a tight particle distribution.Weighting Agents for Density Customization
Whether it's barite, hematite, or other heavy materials, micro silica mixes well without destabilizing the slurry. Engineers can increase or decrease density as needed without sacrificing strength or durability.
This broad compatibility means micro silica can be used across the full spectrum of cementing operations—from shallow surface casing jobs to deep reservoir completions.
Sustainability and Environmental Impact
With the industry under increasing pressure to reduce its carbon footprint, micro silica offers some sustainability advantages:
Byproduct Utilization: As a byproduct of silicon alloy manufacturing, it contributes to waste reduction.
Enhanced Cement Durability: Longer-lasting wells mean fewer repairs and workovers, lowering overall emissions.
Reduced Water Requirement: Better particle packing allows for lower water content in the slurry.
These factors make undensified micro silica not only an effective additive but also an environmentally responsible one.
Partner with Trident Energy International for High-Performance Micro Silica Solutions
At Trident Energy International, we specialize in delivering high-purity, undensified micro silica engineered for critical oil well cementing applications. Our product undergoes rigorous quality control to ensure optimal particle size distribution, pozzolanic activity, and consistency—making it the preferred choice for challenging environments such as HPHT wells, deepwater operations, and gas migration zones. Backed by deep industry expertise and a commitment to technical excellence, we help our clients achieve superior cement integrity, enhanced durability, and long-term well performance. When it comes to oilfield-grade micro silica, Trident Energy International brings you the best version—reliable, performance-driven, and globally trusted.
Final Thoughts
Undensified micro silica has come a long way from being an industrial byproduct to becoming a key performance enhancer in oil well cementing. Its ability to increase strength, reduce permeability, prevent gas migration, and improve durability makes it an irreplaceable material in the oil and gas sector.
Whether you're drilling onshore or offshore, dealing with HPHT conditions, or cementing shallow wells, undensified micro silica offers a versatile, reliable, and cost-effective solution.
As the industry continues to evolve with a focus on safety, performance, and sustainability, additives like undensified micro silica will only grow in importance.
For oilfield professionals, understanding how to leverage this powerful material could be the difference between a well that lasts decades and one that fails prematurely. The future of oil well integrity might just lie in a handful of silica dust.
Frequently Asked Questions (FAQs)
Q1. Is undensified micro silica safe to handle?
Yes, it is generally safe but should be handled using standard industrial hygiene practices. Dust masks and protective gear are recommended.
Q2. Can it be used in both onshore and offshore wells?
Absolutely. Undensified micro silica has proven effective in both environments.
Q3. What is the typical dosage in cement slurries?
It varies, but typically ranges between 5% to 15% by weight of cement (BWOC).
Q4. Is there a shelf life for undensified micro silica?
If stored properly in dry conditions, it can be used for extended periods without significant degradation.
Q5. Does it affect pumpability?
When used with proper dispersants, it actually improves the rheological properties of cement slurries.