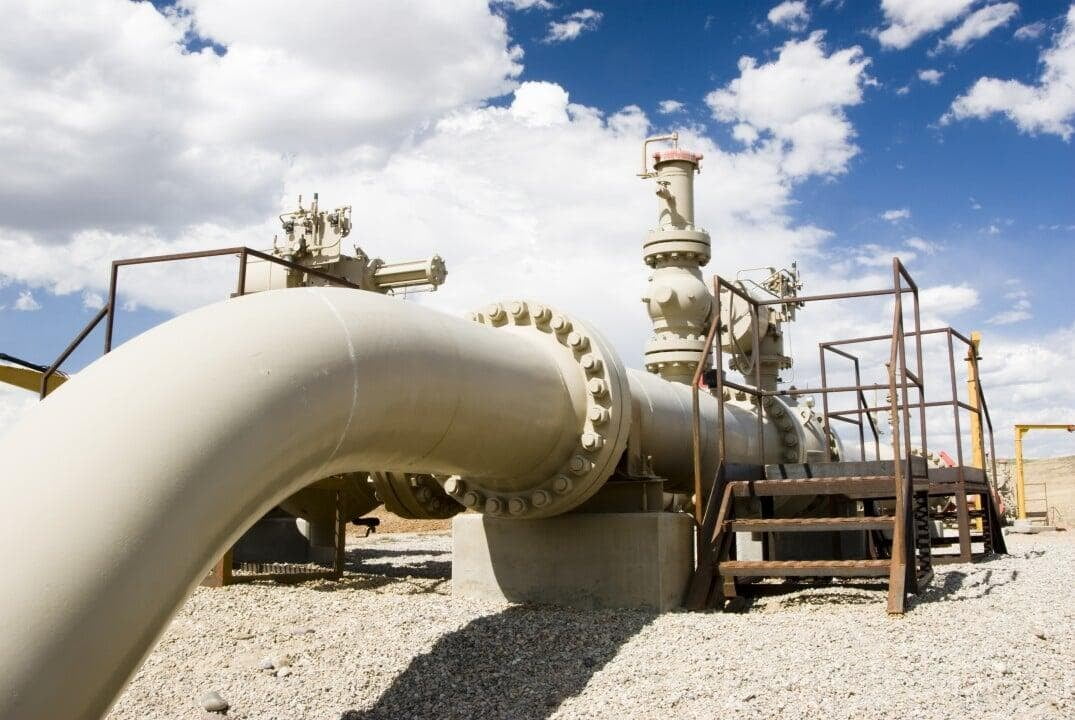
What are Drag Reducing Agents and Why Are They Important?
Drag reducing agents are chemical compounds used to lower frictional resistance within pipelines carrying crude oil, natural gas, or other fluids. When a liquid or gas flows through a pipeline, it experiences friction, especially in high-velocity or turbulent flow conditions. This frictional drag limits flow rates, demands higher energy for transportation, and increases operational costs.
When DRAs are injected into a pipeline, they interact with the fluid to streamline the flow, significantly reducing frictional drag. As a result, pipelines can operate at higher capacities, often with less energy input. This can translate to both operational savings and a reduced environmental footprint—critical goals for modern oil and gas companies.
Types of Drag Reducing Agents
Several types of DRAs are commonly used in the oil and gas sector, each suited to specific pipeline conditions and fluid characteristics:
Polymeric DRAs: Derived from high-molecular-weight polymers like polyalphaolefins, these are the most commonly used DRAs in crude oil pipelines. They’re particularly effective in reducing turbulent flow, which is prevalent in long-distance pipelines.
Surfactant-based DRAs: These agents are versatile, working well in both oil and water pipelines. They alter the surface tension between fluid layers, allowing smoother flow. Their ability to adapt to various fluid types makes them popular for multi-phase pipelines.
Suspension DRAs: These are DRAs in solid or particulate forms, ideal for pipelines with unique flow patterns or where a slow, controlled release of DRA is preferred.
Each type has its advantages depending on the application, fluid type, and specific pipeline characteristics. Proper selection of DRAs can significantly enhance performance, reduce operational interruptions, and cut costs.
Benefits of Using DRAs in Oil and Gas Pipelines
Benefits of Using DRAs in Oil and Gas Pipelines
The strategic application of DRAs brings various benefits that align with the industry’s drive for efficiency and sustainability:
Enhanced Pipeline Capacity: By reducing friction, DRAs allow more fluid to flow through the pipeline, effectively increasing capacity without costly infrastructure upgrades. For operators, this means they can move larger volumes of crude or gas without additional pumping stations.
Lower Operating Costs: DRAs can reduce the energy needed for pumping by up to 40%, leading to substantial cost savings. By enabling lower energy consumption, companies can minimize fuel and electricity expenses—a critical advantage given the high costs associated with energy use in pipeline operations.
Reduced Carbon Emissions: Lower energy requirements translate directly to lower emissions, contributing to sustainability goals. For companies committed to environmental responsibility, DRAs offer a way to achieve greener operations without sacrificing performance.
Increased Flexibility and Responsiveness: DRAs enable pipelines to adapt to fluctuations in demand, supporting flow adjustments without compromising efficiency. This flexibility is especially valuable in times of peak demand, or when transporting oil from remote or offshore locations.
Strategic Applications of DRAs
Strategic Applications of DRAs
The benefits of DRAs make them a powerful tool in several oil and gas applications:
Enhanced Oil Recovery (EOR): In mature fields, maintaining sufficient pressure to continue production is crucial. DRAs help by reducing resistance within wellbores, enabling more oil to be extracted efficiently.
Offshore Pipelines: Offshore pipelines face unique challenges, including limited maintenance access and high flow demands. DRAs in offshore pipelines reduce the need for additional pumping systems, supporting reliable and low-cost transportation in deep-sea environments.
Multi-phase Pipelines: Pipelines transporting a combination of oil, gas, and water are particularly challenging due to fluctuating flow conditions. Surfactant-based DRAs work well in such setups, ensuring a smoother flow and reducing separation issues that can otherwise lead to blockages or downtime.
Selecting the Right DRA for Maximum Efficiency
Selecting the Right DRA for Maximum Efficiency
Choosing the appropriate DRA requires a deep understanding of the pipeline’s physical and operational conditions. Key factors include:
Pipeline Length and Diameter: Longer pipelines with larger diameters generally benefit from DRAs with long-lasting effects and high efficacy in turbulent flow conditions.
Crude Oil Properties: Different oils have unique viscosities, temperatures, and compositions, which can influence how well a DRA performs. High-viscosity oils may require more potent polymeric DRAs, while lighter oils may benefit from surfactant-based agents.
Environmental Regulations: With increasing scrutiny on chemical additives, it’s important to select DRAs that are environmentally friendly and comply with local and international standards.
Economic Impact and Cost-Benefit Analysis of DRA Use
The economic impact of DRAs can be substantial, often making the initial investment worthwhile. Companies typically perform a cost-benefit analysis that accounts for the reduction in pumping energy costs versus the expense of DRA procurement. For example, a large crude pipeline might save millions annually due to the reduction in energy requirements and maintenance needs.
In many cases, DRAs can help defer capital expenditures on new infrastructure by extending the capacity of existing pipelines. Real-world case studies have shown that DRA use can reduce pipeline expansion needs, allowing for more cost-effective long-term planning.
Addressing Challenges in DRA Applications
Addressing Challenges in DRA Applications
While DRAs provide a range of benefits, there are potential challenges:
DRA Degradation: High temperatures and pressures can break down DRAs over time. Selecting temperature-resistant formulations or employing periodic injection can mitigate this.
Pipeline Material Compatibility: Some DRAs may react with certain pipeline materials, especially at high concentrations. Ensuring compatibility through lab testing and pilot programs can prevent material degradation.
Build-up and Flow Assurance Issues: In low-flow areas, DRA particles can build up, potentially impacting pipeline integrity. To prevent this, operators may use injection systems that allow for precise control of DRA concentration
Future Innovations in Drag Reduction Technology
Future Innovations in Drag Reduction Technology
Looking forward, innovation in DRA technology is pushing boundaries with biodegradable and environmentally friendly options, as well as advanced formulations for multi-phase pipelines. Additionally, artificial intelligence and machine learning tools are being tested to optimize DRA injection based on real-time pipeline conditions, potentially enhancing efficiency even further.
As environmental concerns grow, oil and gas companies are also exploring DRAs that reduce emissions through their entire lifecycle, from production to dispos
Conclusion
In today’s oil and gas landscape, where operational efficiency, cost reduction, and environmental responsibility are key, drag reducing agents have become a strategic asset. By selecting the right DRA and applying it strategically, companies can increase pipeline capacity, lower costs, and improve sustainability—all critical for a competitive and responsible energy sector.
As DRA technology advances, the scope for improved performance will only grow, making it an exciting area for innovation. The thoughtful application of DRAs could well be the difference between ordinary and exceptional pipeline operations in the oil and gas industry.