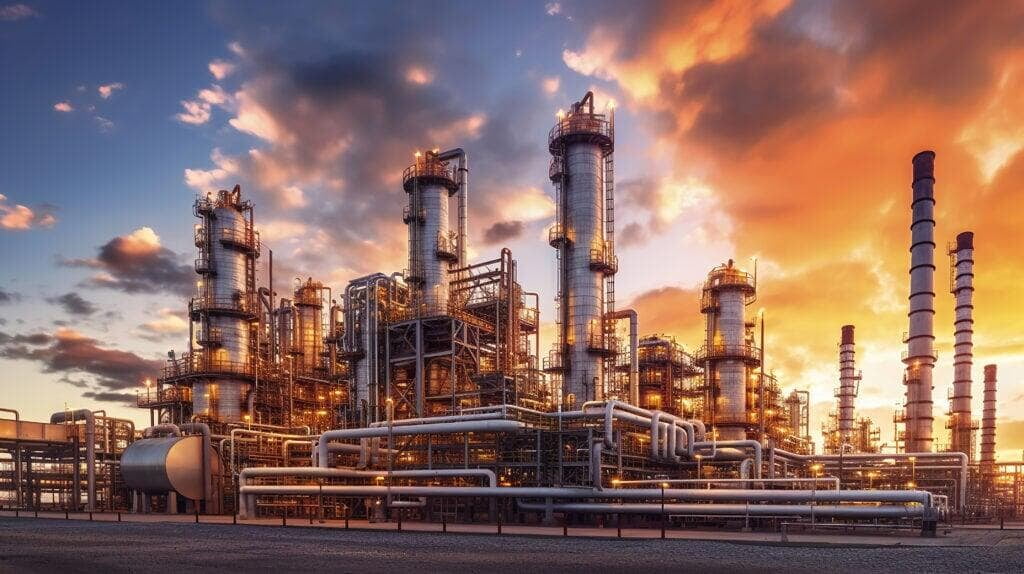
Drilling operations are a cornerstone of the oil and gas industry, as well as in mining and geothermal energy extraction. The efficiency and effectiveness of these operations can significantly impact overall project costs and timelines. One of the most crucial factors influencing drilling performance is the choice and management of drilling fluids. This comprehensive guide will delve into the role of drilling fluid additives, their types, functions, and how they can be optimized to enhance drilling performance.
Understanding Drilling Fluids
Drilling fluids, commonly referred to as drilling muds, are essential for the drilling process. They serve multiple purposes, including:
1. Cooling and Lubricating the Drill Bit: Drilling generates significant heat due to friction and the mechanical work of the drill bit. Drilling fluids help dissipate this heat while also lubricating the drill bit to reduce wear and tear, thereby extending its lifespan.
2. Carrying Cuttings to the Surface: As the drill bit penetrates the earth, it creates rock cuttings that need to be removed efficiently. Drilling fluids help transport these cuttings to the surface, preventing them from accumulating in the wellbore and causing blockages.
3. Maintaining Wellbore Stability: The pressure exerted by drilling fluids helps prevent the collapse of the wellbore and controls the influx of formation fluids. This is particularly important in unstable formations where the risk of wellbore failure is high.
4. Controlling Formation Pressures: Drilling fluids can be designed to exert specific pressures, which is crucial for preventing blowouts and managing formation pressures. This is especially important in high-pressure environments where the risk of formation fluid influx is significant.
5. Providing Data for Geological Analysis: The properties of drilling fluids can provide valuable information about the geological formations being drilled. This data can be used to make informed decisions about drilling strategies and to assess the potential for hydrocarbon recovery.
The Role of Additives in Drilling Fluids
Drilling fluids are typically composed of a base fluid (water, oil, or synthetic) and various additives that enhance their performance. These additives can be categorized based on their functions:
1. Viscosity Modifiers
Viscosity is a critical property of drilling fluids, as it affects the fluid's ability to carry cuttings and maintain wellbore stability. Viscosity modifiers, such as bentonite clay, are commonly used to increase the viscosity of water-based muds. High viscosity helps suspend cuttings and prevents them from settling in the wellbore.
Optimization Tips:
- Regular Viscosity Testing: Conduct regular viscosity tests using a viscometer to ensure the fluid maintains the desired properties. This is crucial for adapting to changing drilling conditions.
- Adjust Concentration: Adjust the concentration of viscosity modifiers based on the specific drilling conditions and formation characteristics. For example, in softer formations, a lower viscosity may be sufficient, while harder formations may require higher viscosity.
2. Fluid Loss Control Agents
Fluid loss control agents are essential for minimizing the loss of drilling fluid into the formation. This is particularly important in permeable formations, where excessive fluid loss can lead to wellbore instability and increased costs. Common fluid loss control agents include starches, polymers, and cellulose derivatives.
Optimization Tips:
- Selection Based on Formation: Select fluid loss control agents based on the specific formation characteristics and expected fluid loss rates. For instance, in highly permeable formations, a more robust fluid loss control agent may be necessary.
- Monitor Fluid Loss: Monitor fluid loss during drilling and adjust the concentration of additives as needed. This can be done by measuring the fluid loss in a standardized test, such as the API fluid loss test.
3. Weighting Agents:
In certain drilling scenarios, particularly when drilling through high-pressure formations, it may be necessary to increase the density of the drilling fluid. Weighting agents, such as barite or hematite, are added to achieve the desired density. This helps control formation pressures and prevents blowouts.
Optimization Tips:
- Density Calculations: Calculate the required density based on the formation pressures and adjust the concentration of weighting agents accordingly. This involves understanding the hydrostatic pressure gradient of the formation.
- Regular Density Monitoring: Regularly monitor the density of the drilling fluid using a mud balance to ensure it remains within the desired range. Adjustments should be made promptly to avoid any pressure-related issues.
4. Lubricants
Lubricants are added to drilling fluids to reduce friction between the drill string and the wellbore, which can lead to improved drilling rates and reduced wear on equipment. Common lubricants include vegetable oils, synthetic oils, and various surfactants.
Optimization Tips:
- Evaluate Frictional Properties: Evaluate the frictional properties of the drilling fluid and adjust lubricant concentrations to achieve optimal performance. This can be done through laboratory testing to determine the coefficient of friction under various conditions.
- Compatibility Checks: Consider the compatibility of lubricants with other additives to avoid adverse reactions that could compromise the fluid's performance. Conduct compatibility tests to ensure that the lubricant does not negatively affect the viscosity or stability of the drilling fluid.
5. pH Control Agents
Maintaining the proper pH level of drilling fluids is crucial for ensuring the stability of other additives and preventing corrosion of drilling equipment. pH control agents, such as caustic soda or soda ash, are used to adjust the pH of the fluid.
Optimization Tips:
- Regular pH Testing: Regularly test the pH of the drilling fluid using pH meters or test strips and adjust as necessary to maintain optimal levels, typically between 8.5 and 10.5 for water-based muds.
- Impact Assessment: Consider the impact of pH on the performance of other additives and the overall drilling fluid system. A pH that is too low can lead to the degradation of certain polymers, while a pH that is too high can affect the performance of fluid loss control agents.
6. Biocides
Biocides are added to drilling fluids to prevent the growth of bacteria and other microorganisms that can lead to the degradation of the fluid and equipment. Common biocides include glutaraldehyde and quaternary ammonium compounds.
Optimization Tips:
- Risk Assessment: Assess the risk of microbial contamination based on the drilling environment, such as the presence of organic matter or stagnant water, and adjust biocide concentrations accordingly.
- Effectiveness Monitoring: Monitor the effectiveness of biocides through microbial testing and consider alternative treatments if microbial growth is detected. Implementing a biocide program that includes regular testing can help maintain fluid integrity.
7. Thinners and Dispersants
Thinners and dispersants are used to reduce the viscosity of drilling fluids, making them easier to pump and handle. These additives help maintain a stable fluid system by preventing the formation of gel structures that can impede flow.
Optimization Tips:
- Viscosity Management: Regularly assess the viscosity of the drilling fluid and adjust the concentration of thinners and dispersants to achieve the desired flow properties. This is particularly important in high-temperature environments where viscosity can increase.
- Compatibility Testing: Ensure that thinners and dispersants are compatible with other additives in the fluid system to prevent any adverse effects on performance.
Conclusion
Optimizing drilling performance through the effective use of drilling fluid additives is essential for successful drilling operations. By understanding the roles and functions of various additives, drilling engineers can make informed decisions that enhance fluid performance, reduce costs, and improve overall drilling efficiency. Regular monitoring and adjustments based on real-time data are crucial for maintaining optimal drilling fluid properties throughout the drilling process. As technology advances, the development of new additives and formulations will continue to play a vital role in the evolution of drilling practices, ensuring that the industry can meet the challenges of increasingly complex drilling environments.