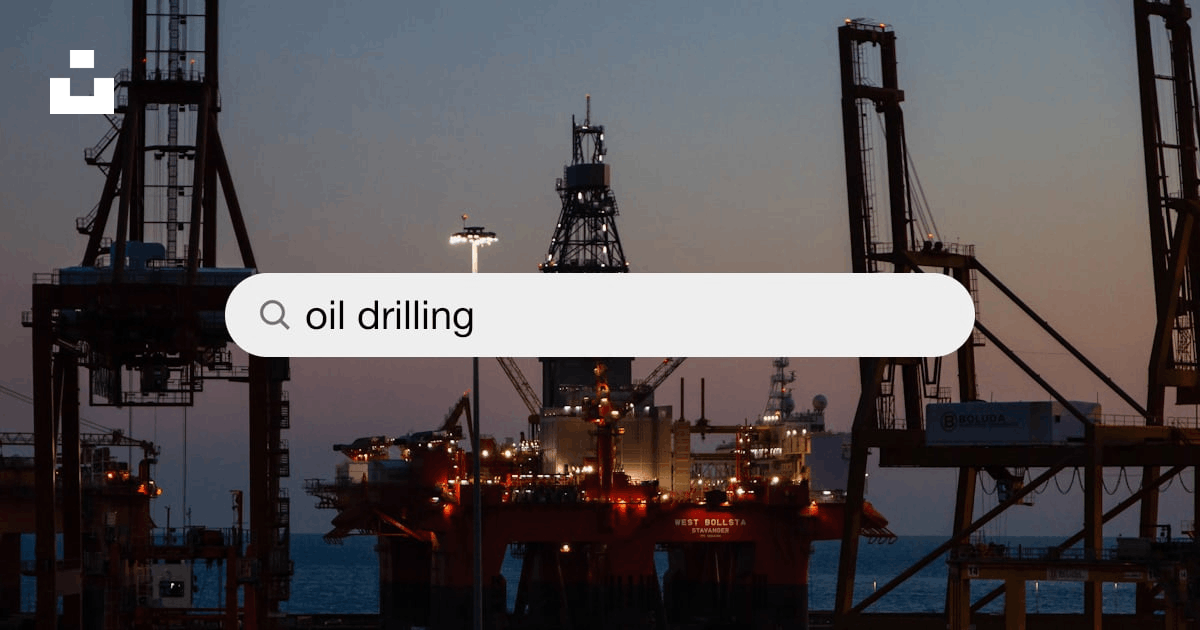
Drilling operations are complex processes that involve penetrating the earth's surface to extract valuable resources such as oil, gas, geothermal energy, or minerals. These operations require a range of specialized chemicals to enhance efficiency, maintain safety, and comply with environmental regulations. Drilling chemicals play a crucial role in optimizing performance by stabilizing wellbores, reducing friction, preventing equipment corrosion, and controlling fluid loss. Additionally, choosing the right chemicals can significantly impact operational costs and sustainability, making it essential to consider factors such as composition, compatibility, and environmental impact. This guide will provide insights into selecting the most suitable drilling chemicals for your specific project, ensuring a balance between performance, cost-effectiveness, and ecological responsibility.
Understanding Drilling Chemicals
Understanding Drilling Chemicals
Drilling chemicals are essential components in drilling fluid formulations, designed to improve the overall efficiency and safety of drilling operations. These chemicals serve multiple purposes, such as stabilizing the wellbore, controlling fluid loss, reducing friction, and protecting drilling equipment from wear and corrosion. They help in maintaining the desired viscosity and flow characteristics of drilling fluids, ensuring smooth circulation and effective removal of cuttings from the well.
Different types of drilling chemicals are used based on specific operational needs. For example:
- Viscosifiers (e.g., bentonite, polymers) enhance the thickness of drilling fluids, improving their ability to carry cuttings to the surface.
- Fluid loss control agents (e.g., starch, PAC, CMC) prevent excessive filtration of drilling fluid into the surrounding formation, preserving wellbore stability.
- Lubricants reduce friction between the drill string and the wellbore, preventing stuck pipe issues and enhancing drilling efficiency.
- Corrosion inhibitors protect drilling equipment, including drill pipes and casings, from damage caused by harsh downhole conditions.
Selecting the right combination of drilling chemicals is crucial to ensuring smooth operations, minimizing environmental impact, and optimizing costs while maintaining high safety and performance standards.
Types of Drilling Chemicals
Types of Drilling Chemicals
This classification provides a structured understanding of the key types of drilling chemicals, each serving a specific purpose to enhance drilling efficiency and wellbore stability. Let’s explore these categories in more detail:
1. Viscosifiers
Function: These additives increase the viscosity of drilling fluids, enabling them to effectively suspend and transport cuttings from the wellbore to the surface. Maintaining the right viscosity is crucial for preventing blockages and ensuring smooth fluid circulation.
Common Chemicals:
- Bentonite – A naturally occurring clay that swells in water to enhance viscosity.
- Xanthan gum – A biopolymer that provides shear-thinning properties, making the mud easier to pump while maintaining its ability to carry cuttings.
- Hydroxyethyl cellulose (HEC) – A water-soluble polymer that improves viscosity, especially in low-solids drilling fluids.
Applications: Used in both water-based and oil-based muds, viscosifiers are essential in deep drilling operations to optimize mud rheology.
2. Fluid Loss Control Agents
Function: These additives minimize the loss of drilling fluid into porous formations by forming a thin, low-permeability filter cake on the wellbore walls. This helps in preventing formation damage and maintaining wellbore stability.
Common Chemicals:
- Starch – A biodegradable fluid loss reducer used in freshwater drilling muds.
- Polyanionic cellulose (PAC) – A widely used polymer that enhances filtration control and viscosity.
- Carboxymethyl cellulose (CMC) – A cost-effective agent that improves mud stability and reduces water loss.
Applications: Essential in maintaining wellbore integrity, especially in highly permeable formations.
3. Shale Inhibitors
Function: These chemicals prevent shale formations from absorbing water, swelling, and breaking apart, which can lead to wellbore instability and drilling complications.
Common Chemicals:
- Potassium chloride (KCl) – A widely used inorganic salt that stabilizes clay formations.
- Polyamines – Organic compounds that effectively inhibit shale swelling.
- Glycols – Water-soluble chemicals that enhance shale stability and reduce hydration.
Applications: Used in water-sensitive formations to ensure the wellbore remains intact throughout the drilling process.
4. Lubricants
Function: Lubricants reduce friction between the drill string and the wellbore, preventing stuck pipe incidents, reducing torque and drag, and improving overall drilling efficiency.
Common Chemicals:
- Vegetable oil-based lubricants – Eco-friendly options that provide effective lubrication.
- Synthetic oil-based lubricants – High-performance lubricants used in challenging drilling environments.
- Graphite – A solid lubricant that enhances wellbore lubrication.
Applications: Particularly important in directional, high-angle, and extended-reach drilling to minimize mechanical resistance.
5. Corrosion Inhibitors
Function: These chemicals protect drill pipes, casings, and other metal components from corrosive damage caused by acidic or saline conditions encountered in drilling environments.
Common Chemicals:
- Amine-based inhibitors – Effective in neutralizing acidic components that cause corrosion.
- Phosphonates – Provide long-term protection against corrosion in high-salinity conditions.
Applications: Widely used in offshore drilling and environments with high levels of CO₂, H₂S, or chlorides.
6. Surfactants & Emulsifiers
Function: These additives help in stabilizing emulsions, reducing surface tension, and improving the wetting properties of drilling fluids, making them more effective.
Common Chemicals:
- Non-ionic surfactants – Improve fluid compatibility and emulsification.
- Anionic emulsifiers – Enhance oil-water emulsion stability in synthetic and oil-based drilling fluids.
Applications: Used in synthetic and oil-based muds to maintain proper emulsion characteristics and improve drilling performance.
Factors to Consider When Selecting Drilling Chemicals
Factors to Consider When Selecting Drilling Chemicals
Choosing the right drilling chemicals depends on multiple factors, including well conditions, environmental impact, and cost-effectiveness. Here are key considerations:
1. Wellbore Conditions
Formation Type: Soft, hard, or fractured formations require different fluid compositions.
Temperature & Pressure: High-temperature and high-pressure (HTHP) wells demand thermally stable chemicals.
Permeability: Low-permeability formations require precise fluid loss control agents.
2. Compatibility with Drilling Fluid System
Drilling chemicals should be compatible with the chosen drilling fluid system, whether water-based, oil-based, or synthetic-based. Incompatibility can lead to undesirable reactions, increasing operational risks.
3. Environmental Regulations
Biodegradability: Ensure chemicals comply with environmental guidelines to minimize ecological impact.
Toxicity Levels: Select non-toxic or low-toxicity chemicals for safer disposal and reduced contamination.
Regional Compliance: Different regions have strict regulatory frameworks, such as the U.S. Environmental Protection Agency (EPA) or European Union standards.
4. Performance & Efficiency
Opt for chemicals that enhance drilling efficiency by improving rate of penetration (ROP), minimizing differential sticking, and ensuring proper hole cleaning.
5. Cost-Effectiveness
While high-performance chemicals may come at a premium, they can reduce overall operational costs by minimizing downtime, improving hole stability, and reducing maintenance requirements.
6. Availability & Logistics
Ensure a steady supply chain for drilling chemicals, especially in remote or offshore locations. Delays in chemical availability can lead to costly interruptions in drilling operations.
Best Practices for Using Drilling Chemicals
Best Practices for Using Drilling Chemicals
To ensure optimal performance, safety, and cost-efficiency in drilling operations, it is essential to follow best practices when using drilling chemicals. These practices help in selecting the right chemicals, maintaining fluid stability, and preventing operational issues.
1. Pre-Drilling Analysis
Before beginning drilling operations, a thorough analysis of the formation and expected downhole conditions is crucial to selecting the right chemical formulations.
- Conduct Formation Evaluation Tests: Analyze the geological characteristics, including porosity, permeability, and shale reactivity, to determine fluid requirements.
- Perform Lab Testing: Assess the compatibility of drilling chemicals with formation conditions and drilling fluids to avoid unexpected reactions or inefficiencies.
- Simulate Field Conditions: Lab-based simulations help predict chemical performance and optimize fluid formulations before actual field application.
2. Proper Mixing & Handling
Accurate mixing and handling of drilling chemicals are essential to maintaining fluid integrity and ensuring their effectiveness.
- Follow Manufacturer Guidelines: Use recommended mixing ratios to prevent overdosing or underdosing, which can impact drilling performance.
- Utilize Automated Mixing Systems: Automated systems ensure precise and consistent mixing, reducing human errors and improving efficiency.
- Store Chemicals Properly: Keep chemicals in a controlled environment (away from moisture, heat, and direct sunlight) to prevent degradation and loss of effectiveness.
3. Continuous Monitoring
Real-time monitoring and adjustments ensure that drilling fluids maintain optimal properties throughout the operation.
- Use Real-Time Monitoring Tools: Advanced sensors and data analytics help track key drilling fluid properties such as viscosity, pH, and filtration rate.
- Adjust Chemical Dosages as Needed: Modify chemical concentrations based on changing downhole conditions to maintain fluid stability and performance.
- Regularly Test Fluid Samples: Field engineers should frequently analyze drilling fluids to detect potential issues early and make necessary corrections.
4. Training & Safety Compliance
Ensuring that personnel are well-trained and that safety protocols are followed minimizes risks associated with handling drilling chemicals.
- Train Field Personnel: Conduct regular training sessions on proper chemical handling, mixing, and disposal procedures.
- Enforce Safety Protocols: Implement safety measures such as proper ventilation, spill containment, and emergency response plans.
- Use Protective Gear: Provide and enforce the use of personal protective equipment (PPE), including gloves, masks, and protective clothing, to minimize exposure to hazardous substances.
Conclusion
Conclusion
Selecting the right drilling chemicals is crucial for optimizing drilling performance, reducing environmental risks, and ensuring cost efficiency. By considering wellbore conditions, fluid compatibility, regulatory compliance, and cost factors, you can make informed decisions that lead to successful drilling operations. Investing in high-quality, tested, and environmentally responsible chemicals will not only enhance drilling efficiency but also contribute to sustainable drilling practices.
Choosing the right drilling chemicals is a strategic decision—make it wisely to achieve operational excellence and long-term success.