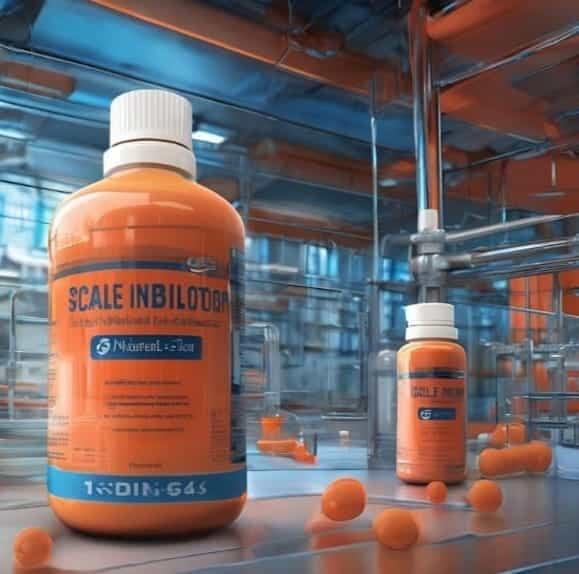
Scale formation is a common problem that occurs in various industrial processes, from cooling towers, boilers, oil extraction field, pipelines and other water handling systems. It occurs when the concentration of certain minerals such as calcium, magnesium, silica exceeds their solubility limits and precipitate out of the solution due to changes in temperature, pressure or evaporation leading to formation of insoluble deposits on the surfaces. Over the period of time the buildup of these deposits causes damage to the equipment, reduces heat transfer efficiency, clog the system, hinders performance and leads to costly maintenance and downtime. It also causes corrosion and other operational issues and of the most effective way to combat these problems is by using scale inhibitors.
What is Scale Inhibitor?
Scale Inhibitors are chemicals designed to prevent the formation of scale or help in breaking down the already formed one. They work by disrupting the crystallization process of mineral salts thus, preventing them from forming insoluble salts and prevents nucleation and growth of crystals. They act as dispersants and prevents scale formation from aggregating and settling on the surface. They act as crystal modifiers and they alter the structure of the scale crystals making them easier to remove.
Importance of choosing the Right Scale Inhibitor:
Importance of choosing the Right Scale Inhibitor:
Selecting the right scale inhibitor is important for preventing these deposits and ensuring optimal performance. These inhibitors will effectively target the specific type of scale and present in the system and provide long lasting protection. Using an ineffective scale inhibitor can lead to persistent scaling issues, increase in operational costs and potential equipment failure. Choosing the right scale inhibitor is essential for effective corrosion and scale management, particularly in industries like oil and gas, water treatment, and chemical processing. Here’s why selecting the correct scale inhibitor is crucial:
Enhanced Equipment Protection: Scale buildup can cause severe damage to pipelines, valves, and other equipment by creating blockages and reducing flow. The right scale inhibitor prevents these mineral deposits from forming, preserving equipment integrity and reducing maintenance costs.
Increased Operational Efficiency: Scale deposits can obstruct fluid flow and reduce heat transfer efficiency, impacting the operational efficiency of the entire system. A suitable inhibitor helps maintain a smooth, uninterrupted flow, ensuring consistent system performance and energy efficiency.
Cost Savings: Using an inappropriate or ineffective scale inhibitor can lead to frequent equipment breakdowns, costly repairs, and downtime. The right inhibitor minimizes scaling issues and reduces the need for frequent cleaning, helping save on maintenance and operational expenses.
Optimized Chemical Usage: Selecting the proper inhibitor allows for optimal chemical dosing, reducing waste and avoiding the use of excess chemicals that could harm equipment or the environment. This targeted approach can improve both operational costs and environmental compliance.
Extended Equipment Lifespan: By preventing scale accumulation, the right scale inhibitor protects components from abrasive wear and corrosion, leading to an extended equipment lifespan. This is especially important for high-value assets in sectors like oil and gas, where equipment replacement costs are high.
Environmental Impact: Many industries now prioritize environmentally friendly operations. Selecting an inhibitor that is biodegradable or less toxic helps minimize environmental damage and meets regulatory standards, allowing companies to maintain compliance with environmental laws.
Regulatory Compliance: Some industries have strict regulatory requirements regarding chemical usage and environmental discharge. Using the correct scale inhibitor helps companies meet these regulations and avoid potential fines or legal issues.
Ultimately, choosing the right scale inhibitor not only preserves the physical assets and improves process efficiency but also contributes to sustainability and compliance goals.
Types of Scale Inhibitors:
Types of Scale Inhibitors:
The following are some of the types of scale inhibitors:
· Magnetic scale Inhibitors - This uses a magnetic field to alter the physical properties of the minerals in the water such as calcium and magnesium. When water flows through the magnetic field, the structure of these minerals changes making them less likely to bind together and form scale on pipes and appliances.
· Electronic Inhibitor- This system emits electronic signals through the water to disrupt the scale formation process.
· Electrolytic – It uses electrolysis to alter the chemical composition of minerals. It introduces a small amount of metal ions (zinc or iron) into the water. This process alters the chemical composition of the water making the minerals less likely to form scale.
· Organic and Inorganic Inhibitors- Organic inhibitors, like carboxylates and sulfonates, offer better performance in diverse conditions and are often used in combination with other inhibitors for enhanced effectiveness. Inorganic inhibitors, such as zinc compounds, are less commonly used but can be effective in specific scenarios.
· Biodegradable Inhibitors- With growing environmental concerns, biodegradable scale inhibitors are gaining popularity. These inhibitors provide effective scale control while minimizing environmental impact. They are particularly useful in industries with stringent environmental regulations.
Factors affecting the choice of Scale inhibitors:
Factors affecting the choice of Scale inhibitors:
Choosing the right scale inhibitor is crucial to ensure efficient and optimal performance. The following are some of the factors to consider before selecting the scale inhibitor:
· Understanding scale forming substances- The first step in choosing the right scale inhibitor is to identify the type of scale that is formed. Different water systems possess different levels and type of scale forming substances like calcium carbonate, calcium sulfate, silica, iron and magnesium compounds. Knowing the composition of these substances in the system will be helpful in choosing the right scale inhibitor.
· Water Quality Analysis- This analysis is helpful in understanding the specific minerals causing scale formations. It focuses on the following key factors:
1. Water Hardness: High levels of calcium and magnesium ions increase the potential for scale formation, so an inhibitor effective against these ions should be chosen.
2. pH Levels: The pH of the water can affect the solubility of scale-forming minerals. For instance, calcium carbonate tends to precipitate out of solution in alkaline conditions, while silica scaling can occur under acidic conditions.
3. Temperature: Some inhibitors are more effective at higher temperatures (as seen in boilers), while others may lose effectiveness in hot water systems.
This will help in understanding the nature of the problem which will help in choosing the right inhibitor.
· Compatibility- It is essential to ensure scale inhibitors are compatible with other minerals used in the system. Incompatibility can lead to unwanted chemical reaction, corrosion or other adverse reactions. Understanding the system’s material compatibility will help in avoiding damages or unexpected reaction with the scale inhibitor.
· Dosage requirement- The dosage of the scale inhibitor depends on the water quality, flow rate, system volume and the desired level of scale prevention. It should be ensured that the scale inhibitor can be dosed easily and accurately based on the system’s needs. Overdosing can lead to unnecessary expenses while underdosing may result in effective scale prevention.
· Environmental Impact- It should be considered before choosing the inhibitor. Preferably the inhibitors should be biodegradable, nontoxic, eco-friendly and it must comply with the regulatory standards in order to minimize harm to the environment. Some inhibitors may require specific disposal methods which should be considered to ensure proper waste management practice.
· Performance Testing and Certifications- It is better to choose that scale inhibitors that have been tested and certified by reputable organisations. These certifications provide assurance that the product meets the industry standards and will perform effectively in the system.
· Maintenance and Monitoring- When choosing the scale inhibitor, the ease of maintenance and monitoring is required to consider. Some inhibitors require regular monitoring and testing to ensure effective scale control, while others may need constant adjustment based on water quality changes or system conditions. It affects the cost and it add expenses.
· Cost effectiveness- It is crucial to consider the long-term cost effectiveness of the scale inhibitor. While it is important to choose an effective product, it should also fit within the budget. Analyzing the overall costs includes the purchase price, dosage requirement, maintenance and potential equipment damage if scale formation occurs. A higher initial investment in a quality scale inhibitor may offer greater value in the long run by reducing the maintenance cost and offering long lasting performance.
Conclusion
Choosing the right inhibitors requires clear understanding of the water quality, the types and effectiveness of the inhibitors, the costs and the impact. With proper selection and implementation, a well-chosen scale inhibitor can extend equipment lifespan, improve system efficiency and will be helpful in avoiding expensive repairs and replacement in the future and will ensure that the system runs smoothly and efficiently.