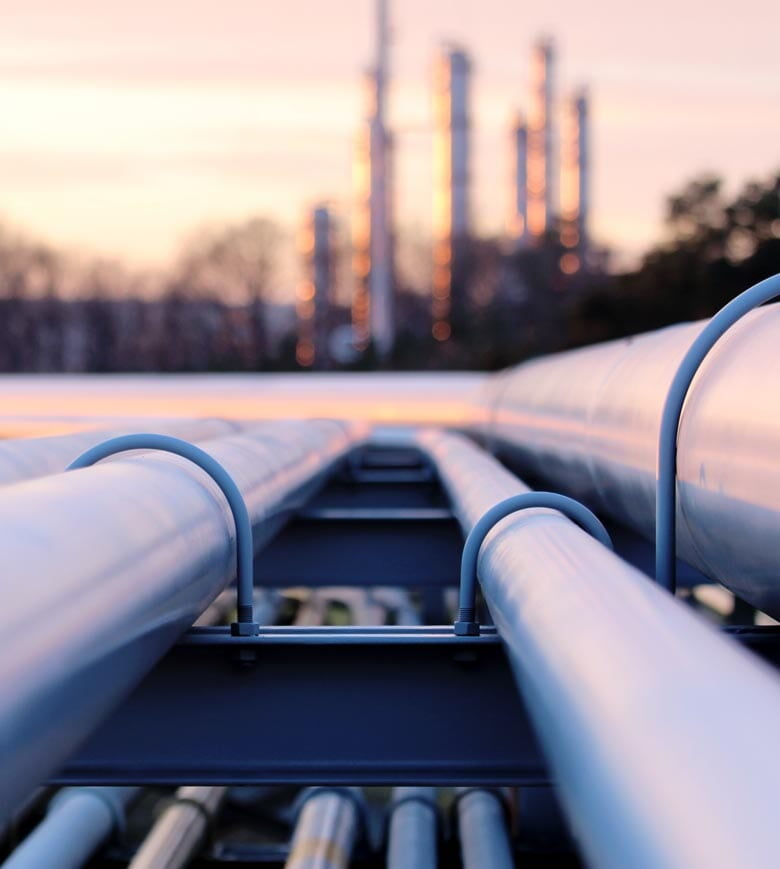
Corrosion inhibitors play a crucial role in the oil and gas industry by protecting pipelines, drilling equipment, and storage facilities from the damaging effects of corrosion. These chemical compounds, when added in small concentrations to the fluid environment, form a protective film on the surface of the metal, thus preventing corrosive reactions with water, oxygen, and other corrosive agents. The use of corrosion inhibitors helps to extend the lifespan of equipment, reduce maintenance costs, and prevent leaks and spills that can lead to environmental hazards. There are various types of corrosion inhibitors used in the industry, including organic inhibitors, which work by adsorbing onto the metal surface, and inorganic inhibitors, which form a protective oxide layer. The selection of a suitable corrosion inhibitor depends on several factors, such as the type of metal, the nature of the corrosive environment, and operational conditions.
What Are Corrosion and Corrosion Inhibitors?
What Are Corrosion and Corrosion Inhibitors?
Corrosion is the natural process through which metals deteriorate due to chemical reactions with their environment. This typically involves the oxidation of metals, leading to the formation of oxides or other compounds. The most familiar form of corrosion is rusting, where iron reacts with oxygen and moisture to form iron oxide. Corrosion can cause significant damage to metal structures and components, leading to mechanical failures, safety hazards, and economic losses, especially in industries like oil and gas, where metal integrity is crucial.
Corrosion inhibitors are chemical substances that, when added in small quantities to an environment where corrosion is likely to occur, significantly reduce the rate of corrosion. They work by forming a protective layer on the metal surface, which prevents corrosive agents like oxygen, water, and salts from reacting with the metal. There are different types of corrosion inhibitors, each suited for specific environments and types of metals. For instance
- Anodic inhibitors: Prevent the anodic reaction (metal oxidation).-Cathodic inhibitors: Slow down the cathodic reaction (reduction of oxygen or hydrogen ions).
-Mixed inhibitors: Affect both anodic and cathodic reactions.
-Volatile inhibitors: Vaporize and protect metal surfaces in confined spaces.
In the oil and gas industry, the use of corrosion inhibitors is essential to maintain the integrity of pipelines, drilling rigs, and storage facilities, thereby ensuring operational safety and efficiency.
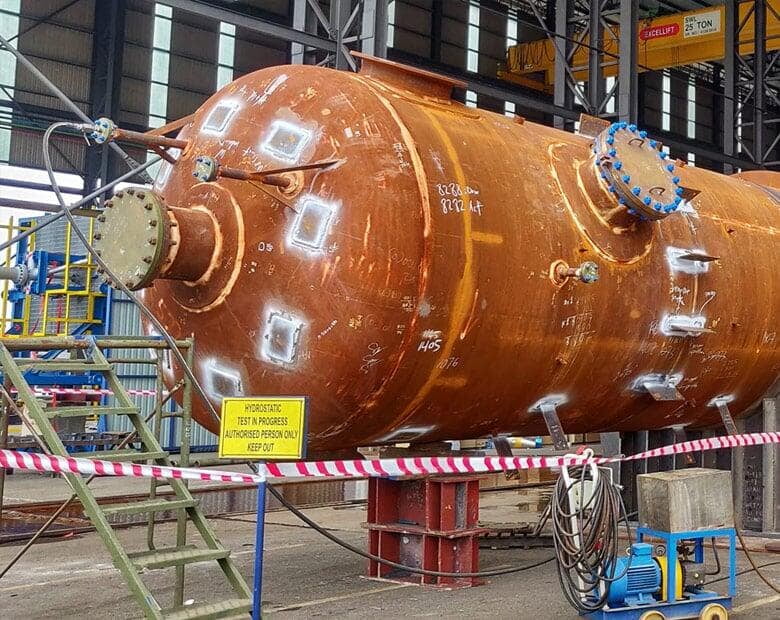
Industrial Applications of Corrosion Inhibitors
Industrial Applications of Corrosion Inhibitors
Corrosion inhibitors find extensive applications in various industries to enhance the durability and lifespan of metal components. In the oil and gas industry, they are used to protect pipelines, drilling equipment, and storage tanks from the harsh, corrosive environments encountered during extraction and processing. In the water treatment industry, corrosion inhibitors are essential for safeguarding metal pipes and infrastructure in water distribution systems. In the automotive industry, they help prevent the rusting of engine parts and body panels, thereby extending the life of vehicles. Additionally, in the manufacturing and construction sectors, corrosion inhibitors are used to protect machinery, tools, and structural components from corrosion, reducing maintenance costs and ensuring operational efficiency.
1.Petroleum Industry
The oil and gas industry represents the largest market for corrosion inhibitors. Inhibitors in this industry protect pipelines, drilling rigs, storage tanks, and other equipment from a corrosive environment. Harsh conditions, coupled with saltwater, hydrogen sulphide, and carbon dioxide, offer an ideal site for corrosion to take place. Corrosion inhibitors extend the life of such assets, assure safe operations, and reduce maintenance costs.
2.Water Treatment
The corrosion inhibitors find wide application in the protection of equipment starting from the boilers, through cooling towers and heat exchangers within a water treatment facility. The systems are normally run at high temperatures and pressures, hence easily subjected to corrosion. Inhibitors like phosphates, silicates, and molybdates help in safeguarding metal surfaces to ensure efficient running water treatment systems.
3.Automotive Industry:
Extensively applied in the car manufacturing industries, corrosion inhibitors protect the vehicle from rust or corrosion. Added to coolants, brake fluids, and fuel systems, they prevent the corrosion of inner components of engines and other parts. In addition, corrosion inhibitors are applied on the outer surfaces of vehicles to protect them against environmental factors like moisture, salt, and pollutants.
4. Aerospace Industry:
Inhibitors in the aerospace industry play a very significant role in keeping aircraft components safe. These inhibitor substances protect aluminium and other metal alloys used in aircraft from moisture and changes in temperature, besides contact with various chemicals, which may cause corrosion. Long-term durability and safety in components could be the guarantee for reliability and excellent performance in air transportation.
5. Marine Industry
The marine industry is much exposed to seawater and other related corrosive marine environments. Saltwater corrosion inhibitors protect ships, offshore platforms, and other associated marine structures. The inhibitors prevent degradation of the metal surface, reduce maintenance costs, and extend the life of marine assets.
6. Construction Industry:
The construction industry inhibitors, basically, prevent the corrosion of reinforced concrete structures, such as bridges and buildings and highways, from corroding. The inhibitors prevent the corrosion of steel rebar embedment within concrete, which may weaken the structure of the construction. Inhibitors prolong the life of these structures and reduce associated maintenance costs.
7. Chemical Processing Industry
Corrosion inhibitors are important in the industries of chemical processing because of the large portfolio of corrosive chemicals in use. The inhibitors protect equipment—from reactors and pipelines to storage tanks—against the action of acids, alkalis, and other chemicals, ensuring smooth and safe operation of the plants for chemical processing.
8.Power Generation
It is applied to very vital parts, including boilers, turbines, and cooling systems, in power generation facilities. The inhibitors prevent the formation of scale and corrosion that will impair efficiency and performance in power generation equipment. The application of corrosion inhibitors in these plants allows them to work more efficiently with less disruption caused by maintenance breaks.
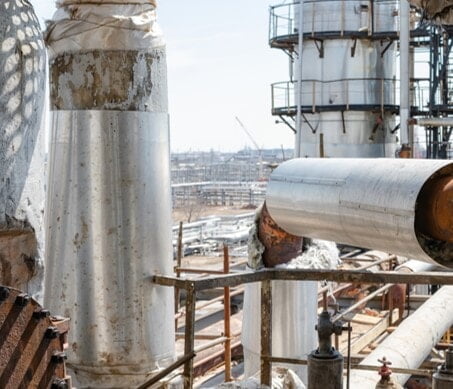
Mechanisms of Corrosion Inhibitors
Mechanisms of Corrosion Inhibitors
The key to the corrosion inhibitor's success lies in its ability to interfere with electrochemical reactions that lie at the heart of the corrosion process. Mechanisms by which corrosion inhibitors work are basically based on:
1. Adsorption: Many corrosion inhibitors work by adsorbing onto the metal surface, forming a protective layer that acts as a barrier against corrosive agents such as oxygen, water, and salts. This layer prevents the direct contact of these agents with the metal, thereby reducing the rate of corrosion.
2. Passivation: Some inhibitors promote the formation of a passive oxide layer on the metal surface. This passive layer is typically a stable and protective film that reduces the metal's reactivity with the corrosive environment.3. Complexation: In this mechanism, inhibitors form stable complexes with metal ions. These complexes are less reactive than the free metal ions, reducing the overall corrosion rate.
4. Precipitation: Certain inhibitors cause the precipitation of compounds that deposit onto the metal surface, creating a protective barrier. These precipitates can be inorganic or organic in nature and serve to block the access of corrosive agents.
5. pH Modification: Some inhibitors work by altering the pH of the environment, making it less conducive to corrosion. For example, increasing the pH in an acidic environment can reduce the availability of hydrogen ions, which are necessary for certain types of corrosion.
6. Oxidation/Reduction: Some inhibitors function by interfering with the electrochemical reactions involved in corrosion. For example, cathodic inhibitors can slow down the reduction reactions (such as oxygen reduction) on the metal surface, while anodic inhibitors can hinder the oxidation reactions of the metal.
These mechanisms can work independently or in combination, depending on the type of inhibitor and the specific environmental conditions. The effectiveness of a corrosion inhibitor is determined by its ability to form a stable, protective layer on the metal surface and its compatibility with the metal and the surrounding environment..
Conclusion
Corrosion inhibitors are thus quite essential in many industries due to their role in saving metal surfaces from the very harmful effects of corrosion. They find their applications in the petrochemical industry, aerospace, marine, automobiles, construction, chemical processing, and power generation. Industries, if familiar with the type and working mechanism of corrosion inhibitors, would be able to make proper use of these chemicals for the safety, durability, and performances of their assets. In this context, the development and optimization of corrosion inhibitors shall play a vital role in combating the continuous challenges raised by corrosion in industrial applications.