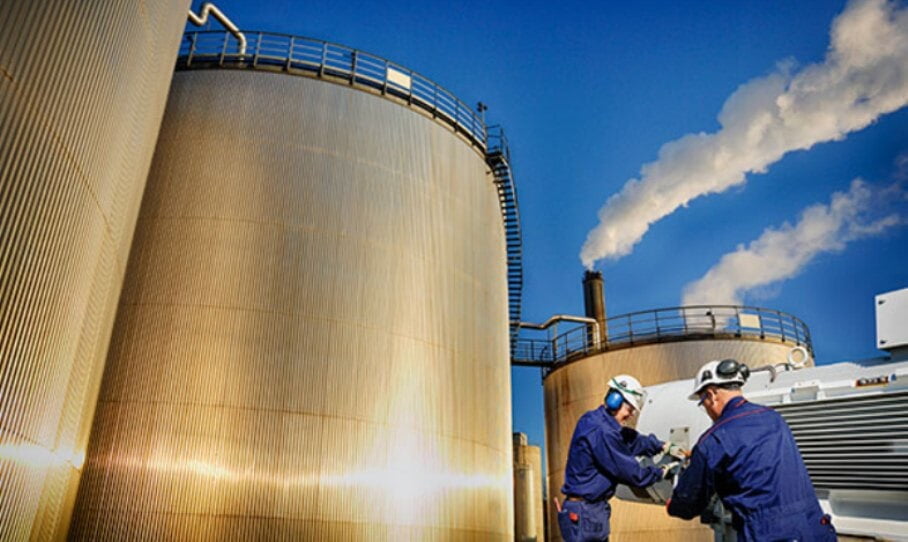
Corrosion is a major concern in the oil and gas industry because the equipment and structures, such as pipelines, storage tanks, and offshore platforms, are constantly exposed to harsh environmental conditions like seawater, humidity, and acidic soils. These factors accelerate the degradation of metal, leading to serious operational challenges, costly repairs, and safety hazards like leaks and spills. Cathodic protection (CP) offers a crucial solution by controlling the electrochemical reactions that cause corrosion. By converting the metal structure into the cathode of an electrochemical cell, CP helps slow or prevent corrosion, safeguarding vital assets and extending their operational lifespan. CP systems are therefore essential in maintaining the efficiency and safety of infrastructure in the oil and gas industry.
Understanding Corrosion and Its Impacts
Understanding Corrosion and Its Impacts
Before discussing cathodic protection, it's important to understand the nature of corrosion in the oil and gas industry. Corrosion occurs when metal reacts with its environment, causing the material to degrade. In the oil and gas industry, pipelines, tanks, and other structures are often exposed to highly corrosive conditions, such as seawater, high humidity, acidic soil, and fluctuating temperatures. These factors accelerate the electrochemical reactions that result in corrosion.
The consequences of corrosion are severe. Corrosion can lead to pipeline leaks, storage tank failures, reduced equipment life, and increased maintenance costs. More critically, corrosion-related incidents can cause environmental disasters, such as oil spills, and jeopardize human safety. Thus, controlling corrosion is vital to ensure the safe and efficient operation of oil and gas infrastructure.
The Principles of Cathodic Protection
The Principles of Cathodic Protection
Cathodic protection is based on the electrochemical principle of converting a corroding metal into a cathode in an electrochemical cell. The process works by reducing the anodic activity of the metal surface, preventing or slowing down corrosion.
Corrosion occurs in metals due to electrochemical reactions, where some areas on the metal surface act as anodes and others as cathodes. The anode is where oxidation occurs, releasing metal ions into the environment, leading to material degradation. Cathodic protection aims to control this process by ensuring that the entire surface of the structure acts as a cathode, where reduction occurs rather than oxidation.
There are two primary methods of achieving cathodic protection: galvanic (or sacrificial) anode systems and impressed current systems. Both methods serve the same goal of reducing or eliminating corrosion, but they work in different ways and are applied in different situations.
Types of Cathodic Protection Systems
Types of Cathodic Protection Systems
There are two main types of cathodic protection systems: galvanic (sacrificial) anode systems and impressed current cathodic protection (ICCP) systems. In a galvanic system, more active metals, like zinc or magnesium, are used as sacrificial anodes that corrode instead of the protected structure. ICCP systems, on the other hand, use an external power source to drive current through inert anodes, providing longer-lasting protection. The choice between these systems depends on factors like the size of the structure, environmental conditions, and the desired duration of protection.
1. Galvanic (Sacrificial) Anode Cathodic Protection
The sacrificial anodes gradually corrode over time, "sacrificing" themselves to protect the steel structure. As long as the anodes are in place and functioning, the structure remains protected. However, the anodes need to be replaced periodically once they become consumed.
Galvanic anode systems are relatively simple and easy to install. They are often used for smaller structures or where power is not readily available, such as underground pipelines, storage tanks, or subsea applications. The limitations of this method include the finite life of the anodes and the need for periodic monitoring and replacement.
2. Impressed Current Cathodic Protection (ICCP)
Impressed current cathodic protection systems are more complex than galvanic systems. In ICCP systems, an external power source (usually a DC power supply or rectifier) is used to drive current through inert anodes (such as mixed metal oxide, graphite, or platinum) to the structure that requires protection. Unlike sacrificial anodes, these inert anodes do not degrade over time.
The power source ensures that a consistent protective current is applied to the structure, making ICCP systems ideal for large structures or highly corrosive environments where more control is needed. ICCP systems are often used for offshore platforms, long pipelines, and large storage tanks where galvanic anodes may not provide sufficient protection.
The advantage of ICCP systems is that they offer long-term protection without the need for frequent anode replacement. However, they require continuous monitoring and maintenance to ensure the power supply and current distribution remain effective.
Applications of Cathodic Protection in the Oil and Gas Industry
Applications of Cathodic Protection in the Oil and Gas Industry
Cathodic protection systems are used in various applications within the oil and gas sector, ensuring the longevity and safety of critical infrastructure.
1. Pipeline Protection
Pipelines are the arteries of the oil and gas industry, transporting crude oil, natural gas, and refined products across vast distances. These pipelines are often buried underground or submerged in water, exposing them to corrosive environments. Cathodic protection is essential for preventing external corrosion, which can cause pipeline leaks or ruptures.
Both galvanic and impressed current systems are used to protect pipelines, depending on the pipeline length, diameter, and environment. For example, buried pipelines in remote areas may rely on galvanic anodes, while large offshore pipelines are typically protected by ICCP systems. Additionally, CP systems are often combined with protective coatings to provide a comprehensive corrosion prevention solution.
2. Storage Tanks
Above-ground and underground storage tanks, commonly used in oil refineries and storage terminals, are exposed to corrosion from both the surrounding soil and the stored contents. Cathodic protection helps prevent corrosion on the tank surfaces in contact with the soil or water.
For underground storage tanks, galvanic anode systems are frequently used. In contrast, large above-ground tanks, especially those located in coastal or highly corrosive environments, often rely on ICCP systems for long-term protection.
3. Offshore Platforms
Offshore oil and gas platforms are exposed to one of the most corrosive environments imaginable: saltwater, humidity, and fluctuating temperatures. The harsh conditions accelerate corrosion, making the use of cathodic protection systems essential for maintaining the structural integrity of these platforms.
Due to the size and complexity of offshore platforms, ICCP systems are commonly used to protect the submerged parts of the structure, including the steel legs, risers, and subsea pipelines. In some cases, galvanic anodes are used for smaller platform components or in combination with ICCP for enhanced protection.
4. Refinery and Processing Plants
Refineries and processing plants are complex facilities where various equipment, pipes, and storage vessels are prone to corrosion due to the handling of crude oil, chemicals, and high temperatures. Cathodic protection is applied to protect tanks, pipelines, and other metallic components from external corrosion.
In refinery applications, impressed current systems are preferred due to the large surface areas that need to be protected. These systems ensure consistent protection, even in areas with fluctuating environmental conditions or high corrosive potential.
5. Subsea Structures
Subsea structures, such as risers, wellheads, and flowlines, are critical components of offshore oil and gas operations. These structures are constantly exposed to the corrosive effects of seawater and marine organisms. Cathodic protection, usually in the form of ICCP systems, is vital for extending the life of these subsea assets.
In some cases, hybrid systems that combine galvanic anodes and ICCP are used to ensure comprehensive protection across different components of subsea infrastructure.
Monitoring and Maintenance of Cathodic Protection Systems
Monitoring and Maintenance of Cathodic Protection Systems
Cathodic protection systems require regular monitoring and maintenance to ensure they continue to function effectively. Monitoring typically involves measuring the potential difference between the protected structure and a reference electrode to ensure the desired level of protection is being achieved.
For galvanic anode systems, periodic inspections are needed to assess the remaining life of the anodes and replace them when necessary. In ICCP systems, regular checks of the power supply, rectifiers, and anodes are required to prevent system failures.
Modern CP systems often incorporate remote monitoring technologies, allowing operators to track system performance in real-time and respond quickly to any issues. This is especially beneficial for protecting pipelines and offshore platforms in remote or difficult-to-access locations.
Conclusion
Cathodic protection is a vital component of corrosion management in the oil and gas industry. By converting metallic structures into cathodes and preventing anodic reactions, CP systems protect pipelines, tanks, offshore platforms, and other critical infrastructure from the detrimental effects of corrosion. The choice between galvanic anode systems and impressed current systems depends on the specific requirements of the application, including the size of the structure, environmental conditions, and desired lifespan of the protection.
By investing in cathodic protection, oil and gas companies can significantly reduce maintenance costs, prevent environmental and safety incidents, and extend the life of their valuable assets.