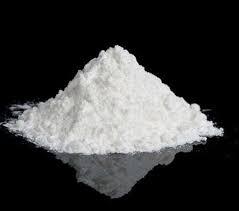
The oil and gas industry is a cornerstone of global energy production, powering economies and supporting countless industries worldwide. To maintain efficiency and productivity in this demanding sector, various chemical additives play a critical role in optimizing key processes such as drilling, completion, and production. Among these, Carboxymethyl Cellulose (CMC) has emerged as a highly versatile and indispensable polymer. Derived from cellulose, CMC is a water-soluble, chemically modified compound that brings unique advantages to oil and gas field operations.
Its adaptability and performance-enhancing properties have made it a preferred choice across a range of applications, including drilling fluid formulations, well stimulation techniques, and enhanced oil recovery (EOR) methods. The polymer's ability to stabilize fluid properties, improve viscosity, and reduce fluid loss under challenging conditions has solidified its reputation as a reliable additive in oilfield operations.
This blog delves deeper into the significance of Carboxymethyl Cellulose in the oil and gas sector. It explores its key applications, highlights its numerous benefits, and discusses the challenges associated with its use. Whether you are an industry professional, a researcher, or simply curious about advanced technologies driving the energy sector, this comprehensive review will shed light on why CMC continues to be a vital component in modern oil and gas operation.
About Carboxymethyl Cellulose:
About Carboxymethyl Cellulose:
Carboxymethyl Cellulose (CMC) is a highly versatile and widely used derivative of cellulose, a natural polymer extracted from plant cell walls. Through a chemical process involving the reaction of cellulose with monochloroacetic acid under alkaline conditions, the cellulose molecule is modified to include carboxymethyl groups (-CH2-COOH). This structural modification enhances the solubility and functionality of cellulose, transforming it into a polymer with unique and highly desirable properties.
CMC appears as a fine, white, odorless, and tasteless powder that dissolves readily in water to form a viscous solution. Its ability to create stable and consistent solutions under a wide range of conditions makes it an invaluable ingredient across numerous industries. The polymer exhibits remarkable thickening, gelling, and stabilizing properties, which enable it to enhance the texture, consistency, and performance of products. Additionally, its non-toxic, biodegradable, and environmentally friendly nature further underscores its appeal as a sustainable material in various applications.
CMC also possesses excellent film-forming and emulsifying capabilities, contributing to its use in diverse fields. In the food industry, it serves as a stabilizer and thickener in products like sauces, dairy items, and baked goods. In pharmaceuticals, it is used as a binder and disintegrant in tablets, as well as a stabilizing agent in liquid medicines. In cosmetics, it helps improve the texture and shelf life of creams, lotions, and toothpaste. Beyond these, its utility extends to industrial applications, including detergents, paper production, textiles, and notably, the oil and gas sector.
In the oil and gas industry, the unique properties of CMC make it a critical additive in drilling fluids, cementing slurries, and enhanced oil recovery methods. Its ability to control fluid loss, stabilize viscosity, and perform under extreme temperature and pressure conditions ensures smoother operations and reduced downtime. Furthermore, its biodegradability and non-toxic nature align with the industry's growing emphasis on environmental sustainability.
The combination of its chemical versatility, functional performance, and environmental compatibility makes CMC an indispensable material in modern industries, particularly in challenging environments like oilfield operations.
Application in Oil and Gas Operations:
Application in Oil and Gas Operations:
Carboxymethyl Cellulose plays a critical role across different stages of oil and gas field operations. Its rheological properties, water retention capabilities, and stability in challenging environments make it a preferred choice for drilling, cementing, and production processes.
· Drilling Fluids: CMC is extensively used as an additive in water-based drilling fluids, drilling fluids play a crucial role in drilling operations. Different grades of CMC are used depending on the specific requirements of the drilling operation, such as viscosity and fluid loss control.CMC modifies the viscosity of drilling muds, contributing to optimal shear-thinning behaviour. This property allows for easy circulation of drilling mud while ensuring adequate suspension of cuttings. Its ability to form a gel-like structure helps to reduce fluid loss while maintaining lubrication, which is essential in high-pressure environments. As an organic polymer, CMC is significant for making drilling operations more environmentally compliant. Its biodegradability reduces the ecological impact of drilling fluids.
· Hydraulic Fracturing: In hydraulic fracturing, CMC acts as a viscosity modifier in the fracturing fluid. As high-pressure fluids create fractures in the reservoir rocks, the thickened fluid ensures effective proppant transport, keeping the fractures open post-operation. CMC enhances the viscosity of fracturing fluids, enabling proppant materials (like sand) to be suspended and transported to the fracture sites effectively. The use of CMC helps create a viscous, gel-like barrier that mitigates fluid loss into the surrounding formations, thereby enhancing recovery rates.
· Enhanced Oil Recovery (EOR): In the quest to extract more oil from reservoirs, Enhanced Oil Recovery (EOR) techniques are crucial. Carboxymethyl Celluloseensures higher oil recovery rates by improving the mobility of oil.By increasing the viscosity of the water used in oil recovery, CMC creates a favourable ratio between the water and oil phases, reducing water break-through and improving sweep efficiency. It stabilizes water-oil emulsions, increasing contact time between the water and oil, which promotes effective displacement.
· Cementing Operations: Cementing is critical for securing casing in a wellbore and isolating formations to prevent fluid migration. Additives like Carboxymethyl Celluloseimprove the performance of cement slurries. It reduces the rate at which water escapes from the cement slurry into the formation, ensuring proper hydration and strength development. It improves the flow properties of cement slurries, making them easier to pump into the wellbore. It stabilizes the suspension of cement particles, ensuring uniform slurry composition. Prevents premature dehydration and formation damage.
Benefits of Carboxymethyl Cellulose:
Benefits of Carboxymethyl Cellulose:
The growing use of Carboxymethyl Cellulose in oilfield operations is attributed to its numerous benefits:
· Environmental Impact: As concerns about environmental sustainability in oil and gas operations grow, the use of biodegradable materials like Carboxymethyl Cellulose is increasingly valuable. The integration of CMC not only reduces environmental hazards associated with traditional synthetic additives but also promotes a more sustainable approach to resource extraction. CMC's natural origin ensures that it can break down in environmental settings, leading to less contamination. It poses minimal risks to aquatic and terrestrial life, making it an attractive option for environmentally conscious companies.
· Cost-Effectiveness: The use of Carboxymethyl Cellulose can lead to significant cost savings in oil and gas operations, both in terms of material costs and operational efficiency. CMC's effectiveness as a thickening agent means that smaller quantities can be used to achieve the desired viscosity compared to other synthetic polymers. This can lead to lower material costs over time. By improving the performance of drilling fluids and oil recovery process, it can enhance overall operational efficiency. This can result in reduced drilling times, lower energy consumption, and increased production rates all of which contribute to cost savings.
· Stability Under Harsh Conditions: Oil and gas operations often occur under extreme conditions, including high temperatures and pressures. CMC's stability under these conditions is a significant advantage.
CMC maintains its viscosity and performance characteristics even at elevated temperatures, which is crucial for deep well drilling and high-temperature enhanced oil recovery applications. This stability ensures that the fluid properties remain consistent throughout the operation. It can withstand high-pressure environments, making it suitable for use in deepwater drilling and other challenging scenarios. This resilience helps maintain the integrity of the drilling fluid and enhances the overall success of the operation.
Challenges of Carboxymethyl Cellulose:
Challenges of Carboxymethyl Cellulose:
Carboxymethyl Cellulose offers numerous benefits in oil and gas field operations, there are also several challenges and limitations associated with its use some of them are as follows:
· Regulatory and Compliance Issues: As environmental regulations become more stringent, the use of additives like CMC may be subject to increased scrutiny. In some regions, the use of CMC in oil and gas operations may require regulatory approval, which can involve lengthy processes and additional costs.Operators may need to conduct environmental impact assessments to evaluate the potential effects of using CMC in their operations. This can add complexity and time to project planning and execution.
· Potential for Gel Formation: Under certain conditions, CMC can form gels, which may hinder its effectiveness in fluid systems. In high concentrations or specific pH conditions, CMC can form gels that may not be desirable in drilling. This gel formation can lead to difficulties in pumping and may require additional additives to break the gel and restore fluid flow. The presence of gels can alter the flow characteristics of the fluid, potentially leading to blockages or reduced efficiency in proppant transport during hydraulic fracturing operations. Operators must carefully monitor and manage the concentration of CMC to avoid these issues.
· Environmental Concerns with Disposal: While CMC is biodegradable, the disposal of drilling fluids containing CMC can still pose environmental challenges. If not properly managed, the disposal of CMC-laden fluids can lead to contamination of soil and water resources. Operators must ensure that disposal methods comply with environmental regulations to mitigate these risks. The costs associated with the proper disposal of drilling waste can be significant, particularly if specialized treatment or disposal methods are required to handle fluids containing CMC.
Conclusion
Carboxymethyl cellulose is a versatile and valuable additive in oil and gas field operations. Its unique properties make it suitable for a range of applications, from drilling fluids to enhanced oil recovery and hydraulic fracturing. While there are challenges associated with its use, ongoing research and development are likely to enhance its effectiveness and broaden its applications in the industry. As the oil and gas sector continues to evolve, Carboxymethyl cellulose is going to play a significant role in improving operational efficiency and sustainability.